Continuous-type arm group capture mechanism facing a non-cooperative target
A non-cooperative target and continuous technology, which is applied in the field of continuous arm group capture mechanism, can solve the problems of rigid capture mechanism, such as poor compliance, easy to produce large impact, capture failure, etc., to overcome the lack of load and stability, enhance the Overall stiffness, the effect of increasing contact friction
- Summary
- Abstract
- Description
- Claims
- Application Information
AI Technical Summary
Problems solved by technology
Method used
Image
Examples
Embodiment Construction
[0029] The present invention will be further described below in conjunction with the drawings.
[0030] Such as Figure 1 to Figure 7 As shown, a continuous arm group capturing mechanism for non-cooperative targets includes a capturing device 1 and a driving device 2. The capturing device 1 includes nine under-actuated continuous mechanical arms 1-1, each of which is under-actuated continuous The mechanical arm 1-1 includes a silicone sleeve 1-2 with a convex surface, a central frame 1-3, a first driving cord 1-4, and a second driving cord 1-5; the driving device 2 includes a first motor 2- 1. The second motor 2-2, the motor fixing plate 2-3, twelve linear bearings 2-4, six linear bearing guide rods 2-5, the first drive wire fixing plate 2-6, the second drive wire fixing plate 2-7. Drive box cover 2-8, six side panels 2-9, drive box bottom 2-10;
[0031] The middle and both ends of the six linear bearing guide rods 2-5 shown are machined with threads, and shoulders are set at the ...
PUM
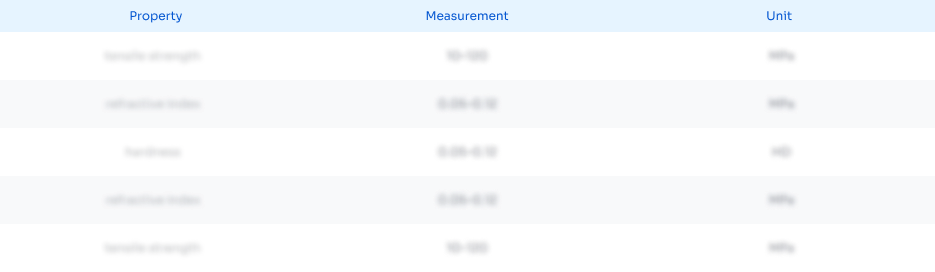
Abstract
Description
Claims
Application Information

- R&D
- Intellectual Property
- Life Sciences
- Materials
- Tech Scout
- Unparalleled Data Quality
- Higher Quality Content
- 60% Fewer Hallucinations
Browse by: Latest US Patents, China's latest patents, Technical Efficacy Thesaurus, Application Domain, Technology Topic, Popular Technical Reports.
© 2025 PatSnap. All rights reserved.Legal|Privacy policy|Modern Slavery Act Transparency Statement|Sitemap|About US| Contact US: help@patsnap.com