High-speed camera calibration system and method
A high-speed camera and calibration system technology, applied in the field of photography, can solve the problems of affecting blasting power, inaccurate time estimation, affecting the development progress of weapon systems, etc.
- Summary
- Abstract
- Description
- Claims
- Application Information
AI Technical Summary
Problems solved by technology
Method used
Image
Examples
Embodiment Construction
[0065] Preferred embodiments of the present invention will be specifically described below in conjunction with the accompanying drawings, wherein the accompanying drawings constitute a part of the application and are used together with the embodiments of the present invention to explain the principles of the present invention.
[0066] An embodiment of the present invention provides a high-speed camera calibration system, such as figure 1 As shown, including calibration board, ranging laser radar, high-speed camera, exposure time and frame loss measurement device and imaging distortion calibration device;
[0067] The calibration plate is a quadrilateral grid-shaped flat plate; a plurality of artificial calibration points are arranged on the grid-shaped flat plate;
[0068] The ranging laser radar generates a high repetition frequency laser signal, measures the position coordinates of the manual calibration point, transmits the coordinate information to the imaging distortion ...
PUM
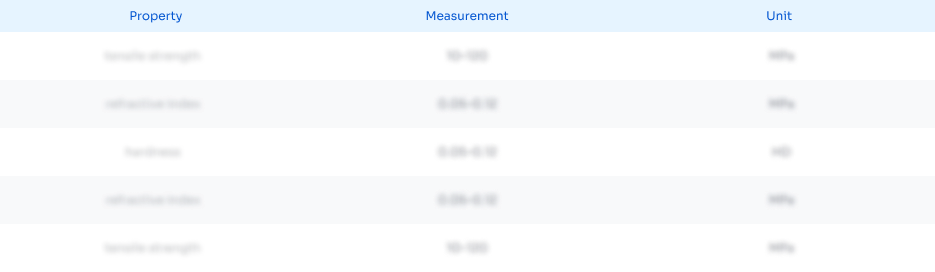
Abstract
Description
Claims
Application Information

- Generate Ideas
- Intellectual Property
- Life Sciences
- Materials
- Tech Scout
- Unparalleled Data Quality
- Higher Quality Content
- 60% Fewer Hallucinations
Browse by: Latest US Patents, China's latest patents, Technical Efficacy Thesaurus, Application Domain, Technology Topic, Popular Technical Reports.
© 2025 PatSnap. All rights reserved.Legal|Privacy policy|Modern Slavery Act Transparency Statement|Sitemap|About US| Contact US: help@patsnap.com