A precision winding device and method for large-diameter dipole coils
A large-diameter coil technology, which is applied in the field of precision winding devices for large-diameter two-pole coils, can solve the problems of lack of tension in the straight side section, increase the crimping mechanism, etc., and achieve convenience, improve winding quality and winding efficiency effect
- Summary
- Abstract
- Description
- Claims
- Application Information
AI Technical Summary
Problems solved by technology
Method used
Image
Examples
Embodiment Construction
[0034] The present invention will be described in detail below in conjunction with the accompanying drawings and specific embodiments.
[0035] A precision winding device for large-diameter dipole coils, including a winding tool base 1, a skeleton 2 of the dipole coil is positioned and fixed on the winding tool base 1; The wire pressing plate 3 on the wire surface; the winding tool base 1 is fixed with multiple sets of pressing device fixing seats 6 along the outer side of the skeleton 2, and one end of the pressing main shaft 4 can slide and rotate on the pressing device fixing seats 6, During the sliding process, the compression tension is provided by the spring A5 installed on the compression main shaft 4, and the stop block 11 is pressed on the pressure plate 3; The block 11 breaks away from the surface of the wire pressing plate 3, and is attached to the outside of the winding tool base 1 by the tension of the spring B10.
[0036] The fixed seat 6 of the crimping device ...
PUM
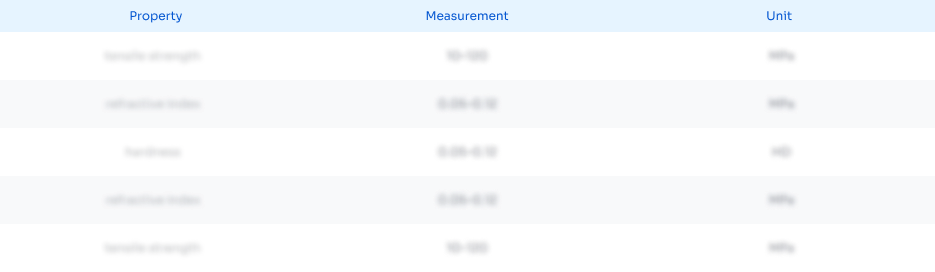
Abstract
Description
Claims
Application Information

- Generate Ideas
- Intellectual Property
- Life Sciences
- Materials
- Tech Scout
- Unparalleled Data Quality
- Higher Quality Content
- 60% Fewer Hallucinations
Browse by: Latest US Patents, China's latest patents, Technical Efficacy Thesaurus, Application Domain, Technology Topic, Popular Technical Reports.
© 2025 PatSnap. All rights reserved.Legal|Privacy policy|Modern Slavery Act Transparency Statement|Sitemap|About US| Contact US: help@patsnap.com