Robot positioning error graded compensation method
A technology of robot positioning and compensation method, applied in manipulators, program-controlled manipulators, manufacturing tools, etc., can solve the problem of large estimation error, and achieve the effect of improving accuracy, improving absolute positioning accuracy, and correct parameter error estimation
- Summary
- Abstract
- Description
- Claims
- Application Information
AI Technical Summary
Problems solved by technology
Method used
Image
Examples
Embodiment 1
[0035] The present invention is realized through the following technical solutions, as figure 1 As shown, a robot positioning error classification compensation method specifically includes the following steps:
[0036] Step S1: Randomly select the theoretical pose P of m sampling points in the area to be compensated s , using a laser tracker to measure the actual arrival pose P of the robot m , to get the end pose error ΔP of the robot before compensation m =P m -P s ;
[0037] Step S2: Establish the kinematic relationship between the connecting rods of the robot to obtain the kinematics model of the robot; establish the kinematics error model of the robot;
[0038] Step S3: Solve the kinematic error model in step S2, obtain the optimal solution of each kinematic parameter error and the corrected kinematic model, and calculate the end pose P of the robot under the corrected kinematic model k ;
[0039] Step S4: The end pose P of the robot under the corrected kinematic mod...
Embodiment 2
[0051] A hierarchical compensation method for robot positioning errors, which analyzes the distribution of robot positioning errors and the mechanism of error sources, and divides the main influencing factors of positioning errors into two types: geometric parameter errors and non-geometric parameter errors. Aiming at the error factors of geometric parameters, a coupling parameter error model is proposed which comprehensively considers the establishment error of the robot frame coordinate system and the error of geometric parameters. Aiming at non-geometric parameter error factors, a residual error model based on spatial similarity is proposed. By studying the hierarchical compensation control mechanism, the robot's hierarchical error compensation based on coupling parameter identification and spatial similarity is realized, and the absolute positioning accuracy of the robot is further improved.
[0052] Specifically include the following steps:
[0053] Step S1: Randomly sel...
Embodiment 3
[0068] Such as figure 1 As shown, a robot positioning error classification compensation method specifically includes the following steps:
[0069] Step S1: Randomly select the theoretical pose P of m sampling points in the area to be compensated s , using a laser tracker to measure the actual arrival pose P of the robot m , to get the end pose error ΔP of the robot before compensation m =P m -P s .
[0070] Step S2: Use the D-H model to establish the kinematic relationship between the connecting rods of the robot to obtain the kinematics model of the robot; according to the theoretical pose P of random sampling points given in step S1 s and the actual pose P measured by the laser tracker m , to establish the robot kinematics error model, the model is established as follows:
[0071] Use the D-H model to establish the kinematic relationship between the connecting rods of the robot. In order to avoid the singularity that occurs when two adjacent axes are parallel or nearl...
PUM
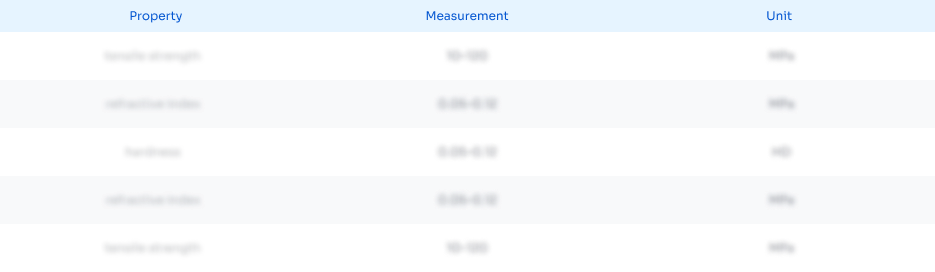
Abstract
Description
Claims
Application Information

- R&D Engineer
- R&D Manager
- IP Professional
- Industry Leading Data Capabilities
- Powerful AI technology
- Patent DNA Extraction
Browse by: Latest US Patents, China's latest patents, Technical Efficacy Thesaurus, Application Domain, Technology Topic, Popular Technical Reports.
© 2024 PatSnap. All rights reserved.Legal|Privacy policy|Modern Slavery Act Transparency Statement|Sitemap|About US| Contact US: help@patsnap.com