Non-uniform arrangement carnassial tooth fixed rotor permanent magnet vernier motor
A vernier motor, non-uniform technology, applied to synchronous motors with stationary armatures and rotating magnets, magnetic circuits, electric components, etc., can solve the problems of being unsuitable for ultra-low speed operation and increasing the magnetic density of the air gap, and achieve low Effects of torque ripple, high torque density, and suppression of cogging torque ripple
- Summary
- Abstract
- Description
- Claims
- Application Information
AI Technical Summary
Benefits of technology
Problems solved by technology
Method used
Image
Examples
Embodiment Construction
[0034] In order to make the technical means, creative features, goals and effects achieved by the present invention easy to understand, the present invention will be further described below in conjunction with specific embodiments.
[0035] refer to Figure 1-10, the specific embodiment adopts the following technical scheme: a non-uniformly arranged split-tooth stator-rotor permanent magnet vernier motor, including a stator and a rotor component, the stator includes a stator yoke 1, a stator large tooth 2, a stator split tooth 3, a winding 4 and stator permanent magnet 5, the rotor includes rotor yoke 6, rotor tooth 7 and rotor permanent magnet 8, the stator large teeth 2 connected with stator yoke 1 are arranged non-uniformly in space, and the stator large teeth 2 split into stator cracks at the end tooth 3, the stator permanent magnet 5 is placed in the slot formed by the stator split tooth 3, the winding 4 is placed in the slot formed by the stator large tooth 2, the rotor ...
PUM
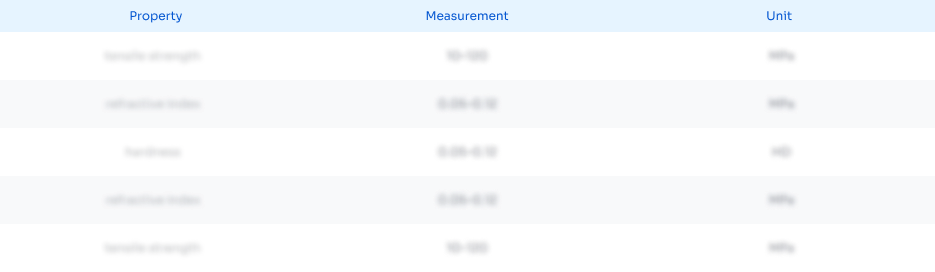
Abstract
Description
Claims
Application Information

- R&D
- Intellectual Property
- Life Sciences
- Materials
- Tech Scout
- Unparalleled Data Quality
- Higher Quality Content
- 60% Fewer Hallucinations
Browse by: Latest US Patents, China's latest patents, Technical Efficacy Thesaurus, Application Domain, Technology Topic, Popular Technical Reports.
© 2025 PatSnap. All rights reserved.Legal|Privacy policy|Modern Slavery Act Transparency Statement|Sitemap|About US| Contact US: help@patsnap.com