Separated machining method of upper die and material pressing plate of stamping die
A stamping die and processing method technology, applied in the field of stamping die upper die and binder plate parts processing, can solve the problems of prolonging the standby time of CNC machine tools, reduce workload and labor intensity, reduce processing operation content, and reduce rework Effect
- Summary
- Abstract
- Description
- Claims
- Application Information
AI Technical Summary
Problems solved by technology
Method used
Image
Examples
Embodiment 1
[0034] processed as Figure 1-4 For the upper mold and pressing plate shown, the following operation steps are adopted:
[0035] The method for processing the stamping die upper die and the binder plate separately comprises the following steps:
[0036] A. Obtain the X and Y coordinates based on the F direction in front of the upper die and the reference base block mounting surface; define the X positive and Y positive directions, and define the guide sliding surface in the X positive and Y negative directions of the upper die base as the reference guide sliding surface. The sliding guide surface of the upper die base in the X negative and Y positive directions is defined as the movable size guide sliding surface, and the bottom pad mounting surface of the upper die is defined as the reference bottom pad mounting surface;
[0037] B. For the binder plate, based on the front F direction of the mold, the guide plate installation surface of the binder plate corresponding to the ...
PUM
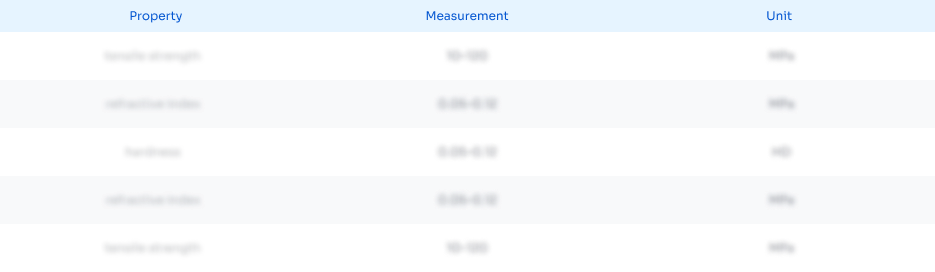
Abstract
Description
Claims
Application Information

- R&D
- Intellectual Property
- Life Sciences
- Materials
- Tech Scout
- Unparalleled Data Quality
- Higher Quality Content
- 60% Fewer Hallucinations
Browse by: Latest US Patents, China's latest patents, Technical Efficacy Thesaurus, Application Domain, Technology Topic, Popular Technical Reports.
© 2025 PatSnap. All rights reserved.Legal|Privacy policy|Modern Slavery Act Transparency Statement|Sitemap|About US| Contact US: help@patsnap.com