An Intelligent Testing System for Linear Displacement Sensor
A technology of linear displacement sensor and test system, applied in the direction of instruments, measuring devices, etc., can solve the problems of high price, difficult processing of collected data, and many types of linear displacement sensors, so as to reduce the cost and improve the calibration efficiency.
- Summary
- Abstract
- Description
- Claims
- Application Information
AI Technical Summary
Problems solved by technology
Method used
Image
Examples
example 1
[0055] Equip the calibrated sensor 2 on the mobile platform of the length measuring machine and measure it:
[0056] (Basic error: ±0.1%, power supply voltage: 12V, voltage output range: 0~10V, interface is 5-pin aviation plug)
[0057] 1) Roughly clamp the sensor 2 to be calibrated to the mobile platform of the length measuring machine through a special clamping device;
[0058] 2) Rotate the fine-tuning mechanism, use the vernier caliper and the level adjustment device to adjust the 2 axis of the calibrated sensor and the standard axis to the same axis;
[0059] 3) Set the power supply voltage to 12V, the signal type of the acquisition device is voltage, and the voltage output range is 0-10V;
[0060] 4) Connect the 5-pin aviation plug to the dedicated interface box, and open the corresponding channel through the software;
[0061] 5) Input the calibration information such as the name, range, specification model, serial number, manufacturer, entrusting customer name and en...
example 2
[0067] Equip the calibrated sensor 2 on the mobile platform of the length measuring machine and measure it:
[0068] (Basic error: ±0.5%, power supply voltage: 24V, current output range: 0~0.5A, interface is 4-pin aviation plug)
[0069] 1) Roughly clamp the sensor 2 to be calibrated to the mobile platform of the length measuring machine through a special clamping device;
[0070] 2) Rotate the fine-tuning mechanism, use the vernier caliper and the level adjustment device to adjust the 2 axis of the calibrated sensor and the standard axis to the same axis;
[0071] 3) Set the power supply voltage to 24V, the signal type of the acquisition device is voltage, and the current output range is 0-0.5A;
[0072] 4) Connect the 4-pin aviation plug to the dedicated interface box, and open the corresponding channel through the software;
[0073] 5) Input the calibration information such as the name, range, specification model, serial number, manufacturer, entrusting customer name and ...
PUM
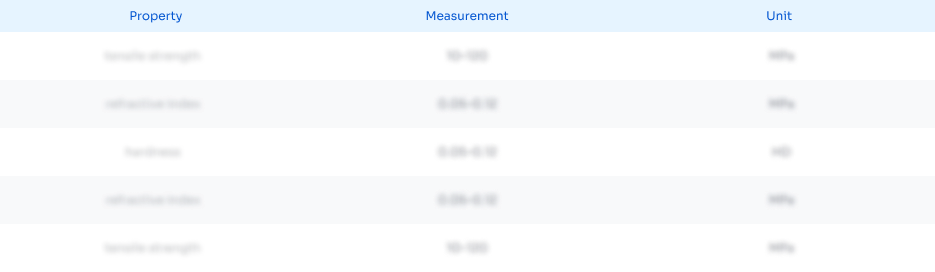
Abstract
Description
Claims
Application Information

- R&D Engineer
- R&D Manager
- IP Professional
- Industry Leading Data Capabilities
- Powerful AI technology
- Patent DNA Extraction
Browse by: Latest US Patents, China's latest patents, Technical Efficacy Thesaurus, Application Domain, Technology Topic, Popular Technical Reports.
© 2024 PatSnap. All rights reserved.Legal|Privacy policy|Modern Slavery Act Transparency Statement|Sitemap|About US| Contact US: help@patsnap.com