Combined mold for oil tube bolt processing
A technology of combining molds and bolts, applied in bolts, manufacturing tools, metal processing equipment, etc., can solve problems such as inability to guarantee quality and low efficiency, and achieve the effect of avoiding export and processing work, reducing production costs, and extending length.
- Summary
- Abstract
- Description
- Claims
- Application Information
AI Technical Summary
Problems solved by technology
Method used
Image
Examples
Embodiment Construction
[0024] Referring to the accompanying drawings, the combined mold for oil pipe bolt processing includes: a first cold heading die, which is used to pre-puncture the wire blank 10 for making oil pipe bolts to obtain a first semi-finished blank 20; Preforming the head and the screw part of the first semi-finished blank 20 and performing secondary punching to obtain the second semi-finished blank 30; Flattening and punching three times to obtain the third semi-finished product blank 40; the fourth cold heading die is used to shape the head of the third semi-finished blank 40 into a hexagonal shape and punch four times to obtain the fourth semi-finished product Blank 50; the fifth cold heading die, for finishing the hexagonal head of the fourth semi-finished blank 50 and the hole of the screw rod to obtain the finished oil pipe bolt 60; the transmission mechanism, for transferring the wire blank to the first A cold heading mold 1, transfer the first semi-finished blank to the secon...
PUM
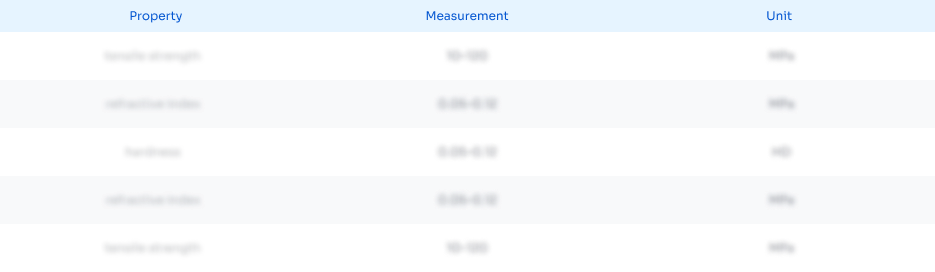
Abstract
Description
Claims
Application Information

- R&D
- Intellectual Property
- Life Sciences
- Materials
- Tech Scout
- Unparalleled Data Quality
- Higher Quality Content
- 60% Fewer Hallucinations
Browse by: Latest US Patents, China's latest patents, Technical Efficacy Thesaurus, Application Domain, Technology Topic, Popular Technical Reports.
© 2025 PatSnap. All rights reserved.Legal|Privacy policy|Modern Slavery Act Transparency Statement|Sitemap|About US| Contact US: help@patsnap.com