Active control method for minimal displacement of magnetic suspension molecular pump rotor
A magnetic levitation rotor, active control technology, applied in pump control, pump, pump components and other directions, can solve problems such as the decline of displacement accuracy, and achieve the effect of improving robustness, easy implementation, and easy parameter adjustment
- Summary
- Abstract
- Description
- Claims
- Application Information
AI Technical Summary
Problems solved by technology
Method used
Image
Examples
Embodiment Construction
[0036] specific implementation plan
[0037] The present invention will be further described below in conjunction with the accompanying drawings and specific embodiments.
[0038] Such as Figure 1-9 As shown, the specific steps of an active control method for the minimum displacement of the magnetic levitation molecular pump rotor in the present invention are as follows:
[0039] (1) if figure 1As shown, the present invention first analyzes the formation mechanism of the unbalanced vibration of the maglev rotor system, establishes the dynamic equation of the maglev rotor for dynamic unbalance, then considers the power amplifier link and the sensor link, and obtains the generalized controlled object mathematical model of the maglev rotor system. Finally, based on Based on the principle of linear active disturbance rejection control and the mathematical model of the generalized controlled object, a linear active disturbance rejection controller with model assistance is design...
PUM
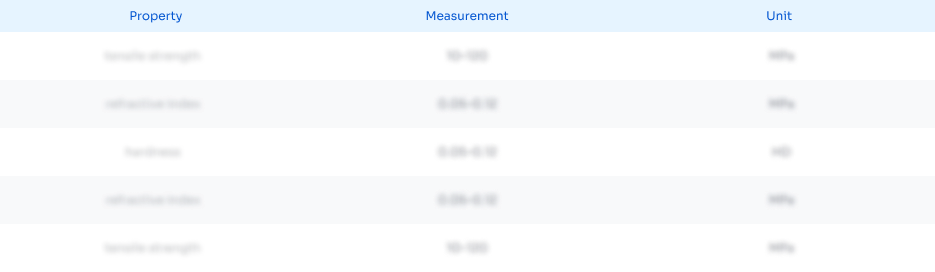
Abstract
Description
Claims
Application Information

- R&D
- Intellectual Property
- Life Sciences
- Materials
- Tech Scout
- Unparalleled Data Quality
- Higher Quality Content
- 60% Fewer Hallucinations
Browse by: Latest US Patents, China's latest patents, Technical Efficacy Thesaurus, Application Domain, Technology Topic, Popular Technical Reports.
© 2025 PatSnap. All rights reserved.Legal|Privacy policy|Modern Slavery Act Transparency Statement|Sitemap|About US| Contact US: help@patsnap.com