Method for desulfurizing kiln tail smoke gas by calcium oxide in kiln tail smoke gas and system thereof
A calcium oxide and sulfur dioxide technology, applied in chemical instruments and methods, separation methods, gas treatment and other directions, can solve the problem that the concentration of calcium oxide cannot meet the requirements of desulfurization, and achieve the effect of increasing the content and reducing the cost.
- Summary
- Abstract
- Description
- Claims
- Application Information
AI Technical Summary
Problems solved by technology
Method used
Image
Examples
Embodiment Construction
[0138] Such as figure 2 As shown, this embodiment provides a method for desulfurizing the kiln tail gas by using calcium oxide in the kiln tail gas. First, the kiln tail gas is taken out from the smoke chamber 00-1, and then separated from the The soot containing calcium oxide can be used for desulfurization agent, and the desulfurization agent is sent to preheater C to desulfurize the kiln tail flue gas.
[0139] In this embodiment, the kiln tail flue gas is firstly taken out from the flue chamber, and then the soot containing calcium oxide is separated from the kiln tail flue gas. The soot containing calcium oxide can be used as a desulfurizer, and the desulfurizer is sent to the Heater is a technical method for desulfurizing kiln tail flue gas. Since the content of calcium oxide in soot is large, it meets the requirements of kiln tail flue gas desulfurization. Therefore, it can effectively desulfurize kiln tail flue gas, and the calcium oxide can be self-sufficient. Self-...
PUM
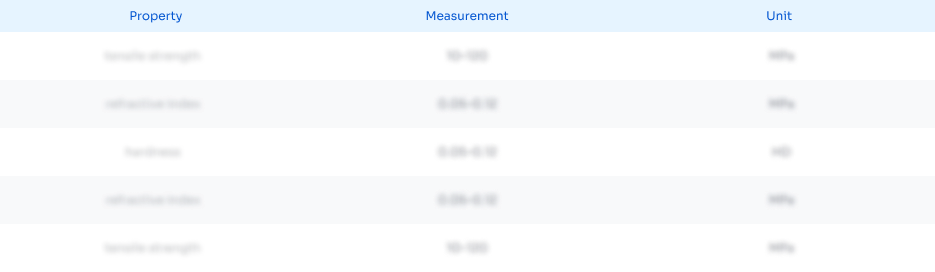
Abstract
Description
Claims
Application Information

- R&D Engineer
- R&D Manager
- IP Professional
- Industry Leading Data Capabilities
- Powerful AI technology
- Patent DNA Extraction
Browse by: Latest US Patents, China's latest patents, Technical Efficacy Thesaurus, Application Domain, Technology Topic, Popular Technical Reports.
© 2024 PatSnap. All rights reserved.Legal|Privacy policy|Modern Slavery Act Transparency Statement|Sitemap|About US| Contact US: help@patsnap.com