A multi-stage pressurized fluorination treatment method for the surface of plastic parts
A technology for fluorination treatment and plastic parts, which is applied in the field of multi-stage pressurized fluorination treatment on the surface of plastic parts. It can solve the problems of surface modification and recovery, surface energy reduction, etc., and achieve surface energy improvement, increase binding force, and surface wetting tension. Value for long-lasting and stable effects
- Summary
- Abstract
- Description
- Claims
- Application Information
AI Technical Summary
Problems solved by technology
Method used
Image
Examples
Embodiment 1
[0041] Embodiment 1: The surface treatment method for plastic parts consists of the following steps:
[0042] 1) Clean and dry the plastic parts;
[0043] 2) Put the dried plastic parts into the airtight reaction chamber of the fluorination equipment, feed nitrogen gas, and replace the air in the reaction chamber 4 times;
[0044] 3) Preheat the internal temperature of the reaction chamber to 40°C, and then pass a mixed gas of fluorine, nitrogen and oxygen to react. The volume ratio of fluorine and nitrogen in the mixed gas is 1:9, and the volume ratio of oxygen It is 1 / 400 of the volume of fluorine gas; the reaction is divided into the following five pressure stages:
[0045] In the first pressure stage, the internal pressure of the reaction chamber is adjusted to 5mbar;
[0046] In the second pressure stage, the internal pressure of the reaction chamber is adjusted to 20mbar;
[0047] In the third pressure stage, the internal pressure of the reaction chamber is adjusted t...
Embodiment 2
[0062] Embodiment 2: The surface treatment method for plastic parts consists of the following steps:
[0063] 1) Clean and dry the plastic parts;
[0064] 2) Put the dried plastic parts into the airtight reaction chamber of the fluorination equipment, feed nitrogen gas, and replace the air in the reaction chamber 4 times;
[0065] 3) Preheat the internal temperature of the reaction chamber to 40°C, and then pass a mixed gas of fluorine, nitrogen and oxygen to react. The volume ratio of fluorine and nitrogen in the mixed gas is 1:9, and the volume ratio of oxygen It is 1 / 400 of the volume of fluorine gas; the reaction is divided into the following five pressure stages:
[0066] In the first pressure stage, the internal pressure of the reaction chamber is adjusted to 8mbar;
[0067] In the second pressure stage, the internal pressure of the reaction chamber is adjusted to 15mbar;
[0068] In the third pressure stage, the internal pressure of the reaction chamber is adjusted t...
Embodiment 3
[0076] Embodiment 3: The surface treatment method for plastic parts consists of the following steps:
[0077] 1) Clean and dry the plastic parts;
[0078] 2) Put the dried plastic parts into the airtight reaction chamber of the fluorination equipment, feed nitrogen gas, and replace the air in the reaction chamber for 5 times;
[0079] 3) Preheat the internal temperature of the reaction chamber to 45°C, and then pass a mixed gas of fluorine, nitrogen and oxygen to react. The volume ratio of fluorine and nitrogen in the mixed gas is 1:8, and the volume ratio of oxygen It is 1 / 300 of the volume of fluorine gas; the reaction is divided into the following 4 pressure stages:
[0080] In the first pressure stage, the internal pressure of the reaction chamber is adjusted to 10mbar;
[0081] In the second pressure stage, the internal pressure of the reaction chamber is adjusted to 30mbar;
[0082] In the third pressure stage, the internal pressure of the reaction chamber is adjusted...
PUM
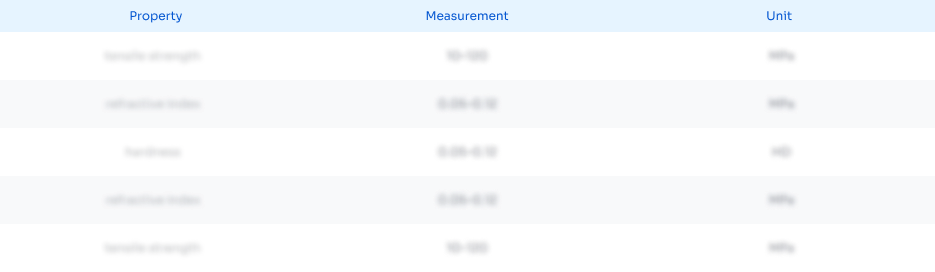
Abstract
Description
Claims
Application Information

- R&D
- Intellectual Property
- Life Sciences
- Materials
- Tech Scout
- Unparalleled Data Quality
- Higher Quality Content
- 60% Fewer Hallucinations
Browse by: Latest US Patents, China's latest patents, Technical Efficacy Thesaurus, Application Domain, Technology Topic, Popular Technical Reports.
© 2025 PatSnap. All rights reserved.Legal|Privacy policy|Modern Slavery Act Transparency Statement|Sitemap|About US| Contact US: help@patsnap.com