Industrial exoskeleton with vibration reduction function
An exoskeleton and industrial technology, which is applied in the field of industrial machinery exoskeleton, can solve the problems of inability to effectively reduce vibration and insufficient deflection degree of freedom, and achieve the effect of high degree of freedom, absorption and buffering of vibration, and auxiliary support stability
- Summary
- Abstract
- Description
- Claims
- Application Information
AI Technical Summary
Problems solved by technology
Method used
Image
Examples
Embodiment 1
[0036] like Figure 1-3 As shown, an industrial exoskeleton with vibration damping function includes an upper trunk support 1 with a balance mechanism 7 installed on the back, and a hip joint 6 is fixedly connected to the lower part of the upper trunk support 1; one side of the hip joint 6 A damping and vibration-absorbing mechanical arm 2 is movably connected, and lower limb assemblies 3 are movably connected to the left and right ends of the hip joint 6 .
[0037] The damping and vibration damping mechanical arm 2 includes a waist arm connecting block 21 , an intermediate connecting block 22 and a clamping device 23 . The right end damping and vibration damping assembly 24-2 is hinged; the free end of the left end damping and vibration damping assembly 24-1 is hinged with one end of the waist-arm connecting block 21, and the other end of the waist-arm connecting block 21 is hinged with the industrial exoskeleton; The free end of the damping and damping assembly 24-2 is clam...
Embodiment 2
[0042] This embodiment is further optimized on the basis of Embodiment 1, such as image 3 and Figure 4 As shown, the middle of the front-end positioning block 241 is also provided with an adjustment installation hole, and a spring adjuster 245 is installed in the adjustment installation hole through a thread; the spring adjuster 245 is connected to one end of the spring damper 243 . The spring damper 243 includes a damping spring and a retractable adjusting rod, the adjusting rod is located inside the spring, and one end of the adjusting rod is connected with the fixing nut on the stud of the spring adjuster 245 .
[0043] When the initial height of the spring damper 243 needs to be adjusted, the spring adjuster 245 is rotated, so that the stud in the technetium spring adjuster 245 drives the fixing nut on it to move up and down, and the fixing nut drives the spring damper 243 to move up and down to complete the initial height. adjust. The spring damper 243 is divided into...
Embodiment 3
[0046] This embodiment is further optimized on the basis of Embodiment 1, such as figure 1 , image 3 , Image 6 As shown, the clamping device 23 includes a connection sleeve 231 and a pan / tilt frame 232, the connection sleeve 231 is clamped with the free end of the right damping and vibration reduction assembly 24, and the bottom of the pan / tilt frame 232 is screwed to the connection Inside the sleeve 231 , a tool fixing block 233 is clamped on the upper part of the pan / tilt frame 232 ;
[0047] The tool fixing block 233 includes an upper semicircular hoop 001, a lower semicircular hoop 002, and a fixing ring 003; the lower semicircular hoop 002 is a semicircular structure with pillars on the left and right sides, and the pillars on the left and right sides are provided with hoop connection grooves There are bosses on the left and right sides of the upper half-circle hoop 001 that match the hoop connecting grooves on the left and right sides of the lower half-circle hoop 00...
PUM
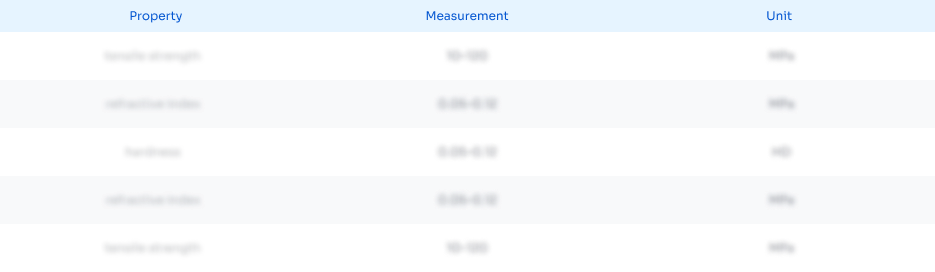
Abstract
Description
Claims
Application Information

- R&D
- Intellectual Property
- Life Sciences
- Materials
- Tech Scout
- Unparalleled Data Quality
- Higher Quality Content
- 60% Fewer Hallucinations
Browse by: Latest US Patents, China's latest patents, Technical Efficacy Thesaurus, Application Domain, Technology Topic, Popular Technical Reports.
© 2025 PatSnap. All rights reserved.Legal|Privacy policy|Modern Slavery Act Transparency Statement|Sitemap|About US| Contact US: help@patsnap.com