Moldflow analysis-based automobile instrument structure optimization method
A technology of automotive instruments and optimization methods, which is applied to instruments, special data processing applications, electrical digital data processing, etc., can solve problems such as low production efficiency and high design costs, and achieve the effects of reducing production efficiency, increasing design costs, and reducing costs
- Summary
- Abstract
- Description
- Claims
- Application Information
AI Technical Summary
Problems solved by technology
Method used
Image
Examples
specific Embodiment approach 1
[0021] Specific embodiment one: a kind of automobile instrument structure optimization method based on Moldflow analysis comprises the following steps:
[0022] Step 1: establish an automobile instrument structure model for the automobile instrument structure through CATIA software;
[0023] Step 2: Import the model established in Step 1 into CADdoctor for diagnosis;
[0024] Step 3: Repair the model according to the diagnosis result obtained in Step 2;
[0025] Step 4: Import the repaired model in Step 3 into CADdoctor for diagnosis;
[0026] Step 5: Repeat Step 3 to Step 4 until there is no error message, then execute Step 6;
[0027] Step 6: Open Autodesk Simulation Moldflow Synergy (mold flow analysis software) and import the file generated in Step 5 into Autodesk Simulation Moldflow Synergy, click the mesh division command to perform double-layer mesh division and grid statistics, and according to the grid division The results of mesh repair;
[0028] Step 7: Set the ...
specific Embodiment approach 2
[0035] Embodiment 2: The difference between this embodiment and Embodiment 1 is that the specific process of repairing the model according to the diagnosis result obtained in Step 2 in Step 3 is as follows:
[0036] According to the diagnosis result obtained in step 2, click the automatic repair function button in the function area of CADdoctor to automatically repair the sharp corners, broken surfaces, incomplete surfaces, rounded corners smaller than R3 and prominent text in the model. For those that cannot be automatically repaired Sharp corners, broken surfaces, incomplete curved surfaces, rounded corners smaller than R3 (radius 3mm), and prominent text After saving the model, open the CATIA software for manual model repair.
[0037] Other steps and parameters are the same as those in Embodiment 1.
specific Embodiment approach 3
[0038] Embodiment 3: The difference between this embodiment and Embodiment 1 or 2 is that the error information in step 5 includes broken surfaces, geometric loss and free edges.
[0039] Other steps and parameters are the same as those in Embodiment 1 or Embodiment 2.
PUM
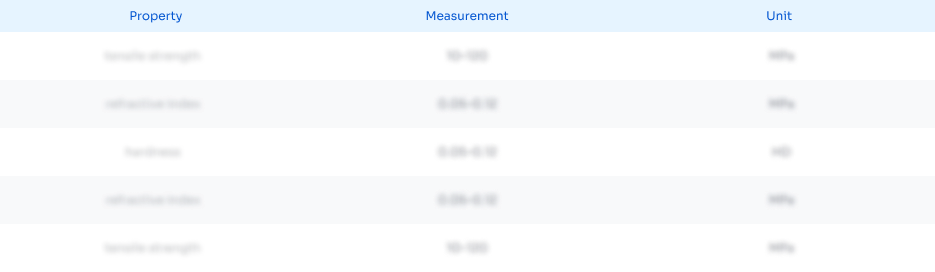
Abstract
Description
Claims
Application Information

- R&D
- Intellectual Property
- Life Sciences
- Materials
- Tech Scout
- Unparalleled Data Quality
- Higher Quality Content
- 60% Fewer Hallucinations
Browse by: Latest US Patents, China's latest patents, Technical Efficacy Thesaurus, Application Domain, Technology Topic, Popular Technical Reports.
© 2025 PatSnap. All rights reserved.Legal|Privacy policy|Modern Slavery Act Transparency Statement|Sitemap|About US| Contact US: help@patsnap.com