Target-free automatic measuring device and method for axis pose of tubular part
A technology for automatic measurement and cylindrical parts, applied in the field of precision measurement, can solve problems such as low precision, inability to eliminate interference, multiple solutions to projection relations, etc., and achieve the effects of improving measurement accuracy, good equipment stability, and large data redundancy
- Summary
- Abstract
- Description
- Claims
- Application Information
AI Technical Summary
Problems solved by technology
Method used
Image
Examples
Embodiment Construction
[0043] Below in conjunction with accompanying drawing and specific embodiment, the present invention is described in further detail:
[0044] refer to figure 1 , a target-free automatic measuring device for the axial position and posture of a cylinder, including a base 1 , a supporting unit 2 , a measuring unit 3 and a control computer 4 .
[0045] Wherein, the support unit 2 includes a support guide rail 21 , a support tray 22 , a transfer screw 23 , and a transfer motor 24 . Both sides of the upper surface of the supporting guide rail 21 are provided with two parallel guide rails, and the lower part is fixed on the base 1 through the mounting seat. The lower surface of the supporting tray 22 is erected on the supporting rail 21 through the rail slider, and the measured cylindrical piece is placed on the upper surface, so that the cylindrical piece can slide along the supporting rail 21 . A transfer lead screw 23 is arranged inside the support guide rail, the axis of the le...
PUM
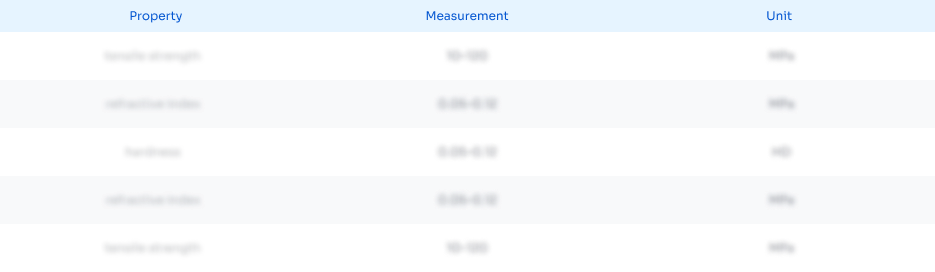
Abstract
Description
Claims
Application Information

- R&D
- Intellectual Property
- Life Sciences
- Materials
- Tech Scout
- Unparalleled Data Quality
- Higher Quality Content
- 60% Fewer Hallucinations
Browse by: Latest US Patents, China's latest patents, Technical Efficacy Thesaurus, Application Domain, Technology Topic, Popular Technical Reports.
© 2025 PatSnap. All rights reserved.Legal|Privacy policy|Modern Slavery Act Transparency Statement|Sitemap|About US| Contact US: help@patsnap.com