A flexible upper limb exoskeleton robot drive system
An exoskeleton robot and drive system technology, which is applied in manipulators, program-controlled manipulators, manufacturing tools, etc., can solve the problems of poor movement flexibility, poor adaptability, and large volume, and achieve large workload, light weight, and reduced volume and quality Effect
- Summary
- Abstract
- Description
- Claims
- Application Information
AI Technical Summary
Problems solved by technology
Method used
Image
Examples
specific Embodiment approach 1
[0034] Specific implementation mode one: as Figure 1-8 As shown, the flexible upper limb exoskeleton robot drive system of this embodiment includes a drive device housing 1, a brake 2, a Bowden wire pretension assembly, a drive device main shaft 15, a drive device housing cover 16, a rigid coupling 17, Brush motor 18, two electromagnetic clutches 4, two connectors 6, two harmonic reducers 8, two wire wheels 11 and two Bowden wires 19; On one end, the output shaft of the brushless motor 18 is affixed to one end of the drive device main shaft 15 through a rigid coupling 17, and the drive device main shaft 15 is installed on the drive device housing 1 through two first deep groove ball bearings 3 to drive The other end of the main shaft 15 of the device is installed on the other end of the housing 1 of the driving device through the brake 2. The electromagnetic clutch 4 includes an armature rotor and an anti-rotation plate. The armature rotor is fixed on the main shaft 15 of the...
specific Embodiment approach 2
[0043] Specific implementation mode two: as Figure 5 and Figure 6 As shown, the wire wheel 11 in this embodiment is provided with a wire wheel joint slot 11-1 and a wire wheel winding slot 11-2, and the fixed end of the Bowden wire 19 is connected to the wire wheel joint slot 11-1, and each wire A Bowden wire 19 is wound in the wheel winding slot 11-2. With such a design, the Bowden wire 19 can be fixed at the slot 11-1 of the spool joint, and then wound in the spool winding slot 11-2. Other components and connections are the same as those in the first embodiment.
specific Embodiment approach 3
[0044] Specific implementation mode three: as image 3 , Figure 5 and Figure 6 As shown, the wire wheel 11 of this embodiment is provided with a flange, and the flange is uniformly processed with a plurality of shoulder through holes along its circumferential direction. The flange of the wire wheel 11 is fixedly connected to the corresponding harmonic wave by a plurality of bolts. On the steel wheel of speed reducer 8. Such a design facilitates the wire wheel 11 to be fixedly connected to the corresponding steel wheel of the harmonic reducer 8 through bolts. Other compositions and connections are the same as those in Embodiment 1 or 2.
PUM
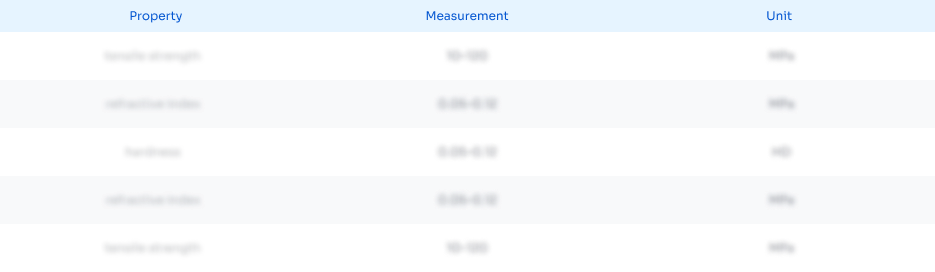
Abstract
Description
Claims
Application Information

- Generate Ideas
- Intellectual Property
- Life Sciences
- Materials
- Tech Scout
- Unparalleled Data Quality
- Higher Quality Content
- 60% Fewer Hallucinations
Browse by: Latest US Patents, China's latest patents, Technical Efficacy Thesaurus, Application Domain, Technology Topic, Popular Technical Reports.
© 2025 PatSnap. All rights reserved.Legal|Privacy policy|Modern Slavery Act Transparency Statement|Sitemap|About US| Contact US: help@patsnap.com