Liquor prepared through Chinese koji saccharification and yeast fermentation and brewing process of liquor
A technology of saccharification of small koji and fermentation of large koji, applied in the field of food processing, can solve the problems of unsuitable production technology, long fermentation cycle, small temperature difference between day and night, etc., achieve the effect of mellow and long taste, shorten the fermentation cycle, and harmonize all flavors
- Summary
- Abstract
- Description
- Claims
- Application Information
AI Technical Summary
Problems solved by technology
Method used
Image
Examples
Embodiment 1
[0028] Material selection: select high-quality raw materials with full particles, uniform size, and heavy metal and pesticide residues that meet the standards;
[0029] Ingredients: Weigh 40kg sorghum, 20kg rice, 8kg wheat, 25kg corn, 10kg glutinous rice and mix them evenly;
[0030] Soaking material: Put the prepared raw materials into the soaking grain tank, add water to wash twice, remove suspended solids, precipitated sand and mildewed raw materials, and then add 80-85°C water at a mass ratio of 1:1. Soak in hot water for 4 hours, and drain the hot water after soaking;
[0031] Initial steaming: Put the soaked raw materials into the steam pot and cook for 1.5 hours. During the cooking process, the pressure of 0.04MPa is maintained. After cooking, the raw materials are stewed in hot water at 90°C. The water consumption of the stewed materials should be 10cm higher than the surface of the raw materials. As the standard, the duration of stewing is subject to the fact that th...
Embodiment 2
[0043] Material selection: select high-quality raw materials with full particles, uniform size, and heavy metal and pesticide residues that meet the standards;
[0044] Ingredients: Weigh 35kg sorghum, 15kg rice, 5kg wheat, 20kg corn, 5kg glutinous rice and mix well;
[0045] Soaking material: Put the prepared raw materials into the soaking grain tank, add water to wash twice, remove suspended solids, precipitated sand and mildewed raw materials, and then add 80-85°C water at a mass ratio of 1:1. Soak in hot water for 3 hours, and drain the hot water after soaking;
[0046] Initial steaming: Put the soaked raw materials into the steam pot and cook for 1.8 hours. During the cooking process, maintain a pressure of 0.05MPa. After the cooking is completed, stew the raw materials with hot water at 85°C. The water consumption of the raw materials should be 8cm higher than the surface of the raw materials. As the standard, the duration of stewing is subject to the fact that the mate...
Embodiment 3
[0057] Material selection: select high-quality raw materials with full particles, uniform size, and heavy metal and pesticide residues that meet the standards;
[0058] Ingredients: Weigh 45kg sorghum, 25kg rice, 10kg wheat, 30kg corn, 15kg glutinous rice and mix them evenly;
[0059] Soaking material: Put the prepared raw materials into the soaking grain tank, add water to wash twice, remove suspended solids, precipitated sand and mildewed raw materials, and then add 80-85°C water at a mass ratio of 1:1. Soak in hot water for 5 hours, and drain the hot water after soaking;
[0060] Initial steaming: Put the soaked raw materials into the steam pot for 2.5 hours, and maintain a pressure of 0.03MPa during the cooking process. After the cooking is completed, stew the raw materials with hot water at 95°C. The water consumption of the raw materials should be 8cm higher than the surface of the raw materials. As the standard, the duration of stewing is subject to the fact that the m...
PUM
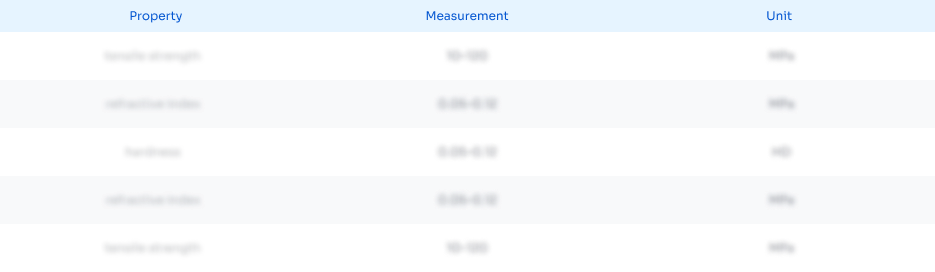
Abstract
Description
Claims
Application Information

- R&D
- Intellectual Property
- Life Sciences
- Materials
- Tech Scout
- Unparalleled Data Quality
- Higher Quality Content
- 60% Fewer Hallucinations
Browse by: Latest US Patents, China's latest patents, Technical Efficacy Thesaurus, Application Domain, Technology Topic, Popular Technical Reports.
© 2025 PatSnap. All rights reserved.Legal|Privacy policy|Modern Slavery Act Transparency Statement|Sitemap|About US| Contact US: help@patsnap.com