An auxiliary robot for sheet metal processing
A sheet metal and robot technology, which is applied in the field of sheet metal processing, can solve the problems of being unsuitable for bending small-sized workpieces, easily interfering with the bending machine, and large structural size, achieving no-degree-of-freedom redundancy and occupying a large area Small, easy-to-control effects
- Summary
- Abstract
- Description
- Claims
- Application Information
AI Technical Summary
Problems solved by technology
Method used
Image
Examples
Embodiment Construction
[0048] The present invention will be further described in detail below in conjunction with the accompanying drawings and specific preferred embodiments.
[0049] Such as figure 1 As shown, an auxiliary robot applied to sheet metal processing includes a base 10, a slider 20, a large arm 30, a small arm 40, a forearm 50, a rotating shaft and a clamp.
[0050] The base is linear, the bottom of the slider slides along the base line, and a 1-axis joint is formed between the slider and the base, referred to as 1-axis.
[0051] The top of the slider is hinged to the bottom of the boom through 2 axes, the top of the boom is hinged to the rear end of the forearm through 3 axes, and the front end of the forearm is hinged to the rear end of the forearm through 4 axes.
[0052] The axes of the 1-axis, 2-axis, 3-axis and 4-axis are all parallel to each other.
[0053] The rotating shaft is 5 shafts, the bottom of the rotating shaft is rotationally connected with the front end of the forear...
PUM
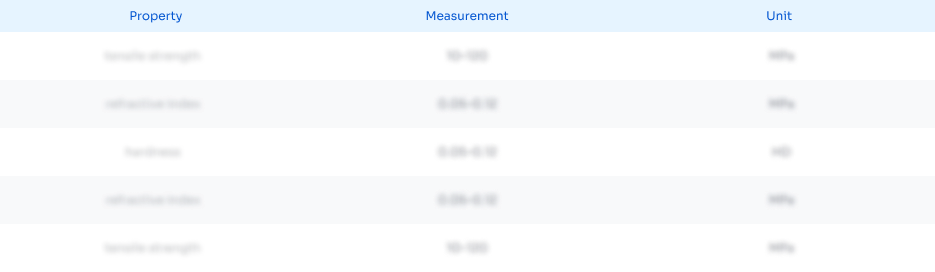
Abstract
Description
Claims
Application Information

- R&D
- Intellectual Property
- Life Sciences
- Materials
- Tech Scout
- Unparalleled Data Quality
- Higher Quality Content
- 60% Fewer Hallucinations
Browse by: Latest US Patents, China's latest patents, Technical Efficacy Thesaurus, Application Domain, Technology Topic, Popular Technical Reports.
© 2025 PatSnap. All rights reserved.Legal|Privacy policy|Modern Slavery Act Transparency Statement|Sitemap|About US| Contact US: help@patsnap.com