Straight module driven wire arrangement device with radial balance mechanism
A linear module and radial balance technology, which is applied in the direction of working accessories, stone processing equipment, manufacturing tools, etc., can solve the problems of poor synchronization of ball screw, influence of wire-passing guide wheel wear and breakage rate, and many matching parts. Achieve the effect of simple structure and ultra-high precision reciprocating motion
- Summary
- Abstract
- Description
- Claims
- Application Information
AI Technical Summary
Problems solved by technology
Method used
Image
Examples
Embodiment
[0017] refer to Figure 1-Figure 4 , a linear module driven cable arrangement with a radial balance mechanism, including a linear module assembly 1 and a radial balance mechanism 2; the radial balance mechanism 2 includes a guide wheel assembly 2-1, a fixed plate 2-2, Connecting seat 2-3, balance plate 2-4, balance plate 2-5, support plate 2-6, axle seat 2-8, bearing 2-9 and axle 2-10, described guide wheel assembly 2-1 is installed on On the fixed plate 2-2, the balance piece 2-5 is fixed on the balance plate 2-4, the fixed plate 2-2, the balance plate 2-4 are connected with the support plate 2-6, and the support plate 2- 6 is fixed on the shaft end of the shaft 2-10, the shaft 2-10 is connected with the shaft seat 2-8 through the bearing 2-9, the shaft seat 2-8 is connected with the connecting seat 2-3, and the radial The balance mechanism 2 is fixed on the linear module assembly 1 through the connecting seat 2-3.
[0018] In this embodiment, the linear module assembly 1 i...
PUM
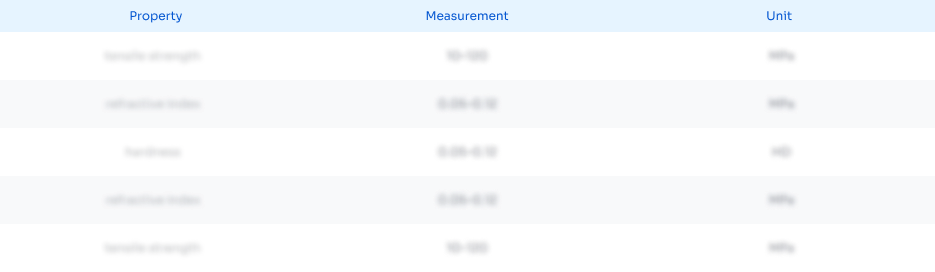
Abstract
Description
Claims
Application Information

- R&D
- Intellectual Property
- Life Sciences
- Materials
- Tech Scout
- Unparalleled Data Quality
- Higher Quality Content
- 60% Fewer Hallucinations
Browse by: Latest US Patents, China's latest patents, Technical Efficacy Thesaurus, Application Domain, Technology Topic, Popular Technical Reports.
© 2025 PatSnap. All rights reserved.Legal|Privacy policy|Modern Slavery Act Transparency Statement|Sitemap|About US| Contact US: help@patsnap.com