Barrel stacking gripper of robot
A robot and bucket stacking technology, applied in conveyors, stacking of objects, de-stacking of objects, etc., can solve the problems of inability to achieve seamless stacking, low energy utilization efficiency, and high cost of use, and achieve multi-purpose flexibility for one machine. work, provide comprehensive work efficiency, and improve the effect of adaptability
- Summary
- Abstract
- Description
- Claims
- Application Information
AI Technical Summary
Problems solved by technology
Method used
Image
Examples
Embodiment Construction
[0013] exist figure 1 , the double dotted line is the gripping state of the gripper. Before grabbing the barrel (9), adjust the lever (8) installed on the main board (1) to a suitable position according to the diameter of the barrel (9) and fix it. When taking out the barrel (9), the baffle cylinder or electric cylinder (3) installed on the main board (1) stretches out to drive the baffle (4) to move the clamping barrel (9) along the guide rail (2), and install it on the baffle (4 ) on the finger cylinder (5) stretches out, drives the finger (7) to swing around the hinge (6), supports the bottom of the barrel (9), and completes the grabbing action. After the robot drives the gripper to the preset position, the finger cylinder (5) retracts, the finger (7) swings around the hinge (6), and the baffle cylinder or electric cylinder (3) retracts to drive the baffle (4) along the guide rail (2) Move backward, the barrel (9) slides to the stacking position, and the robot drives the g...
PUM
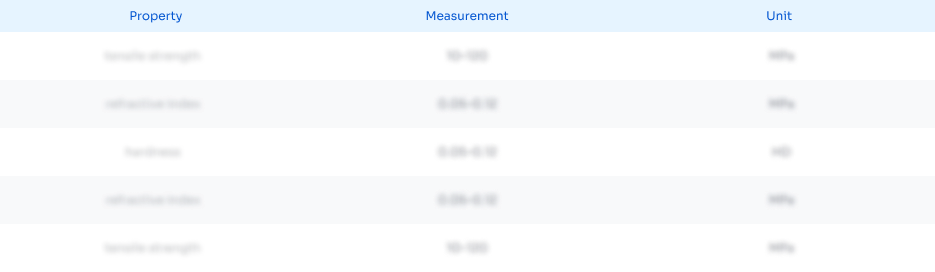
Abstract
Description
Claims
Application Information

- Generate Ideas
- Intellectual Property
- Life Sciences
- Materials
- Tech Scout
- Unparalleled Data Quality
- Higher Quality Content
- 60% Fewer Hallucinations
Browse by: Latest US Patents, China's latest patents, Technical Efficacy Thesaurus, Application Domain, Technology Topic, Popular Technical Reports.
© 2025 PatSnap. All rights reserved.Legal|Privacy policy|Modern Slavery Act Transparency Statement|Sitemap|About US| Contact US: help@patsnap.com