Mechanical arm system
A robotic arm and target technology, applied in the field of robotic arm systems, can solve the problems of lack of measurement, difficulty in adapting to complex scenes and autonomous intelligent operation requirements, insufficient information on irregular objects, etc., to achieve the effect of feedback control
- Summary
- Abstract
- Description
- Claims
- Application Information
AI Technical Summary
Problems solved by technology
Method used
Image
Examples
Embodiment Construction
[0046] Existing robotic arm systems relying on traditional vision and force sensors have become increasingly incapable of application in various fields, and at the same time, it is difficult to adapt to complex scenes and autonomous intelligent operation requirements. In view of this, the present invention provides a manipulator system, which is equipped with a sensing subsystem capable of effectively obtaining environmental information, sensing and identifying features of environmental objects when vision is insufficient or even ineffective, and at the same time incorporates Multi-modal, arrayed, and high-density sensors can measure a variety of tactile comprehensive information, and are sensitive, and can provide sufficient robustness and resolution requirements, giving full play to the characteristics of dexterous operation of redundant robotic arms. Facing diverse and complex environments, improve the fine operability, autonomy and efficiency of human-machine collaboration ...
PUM
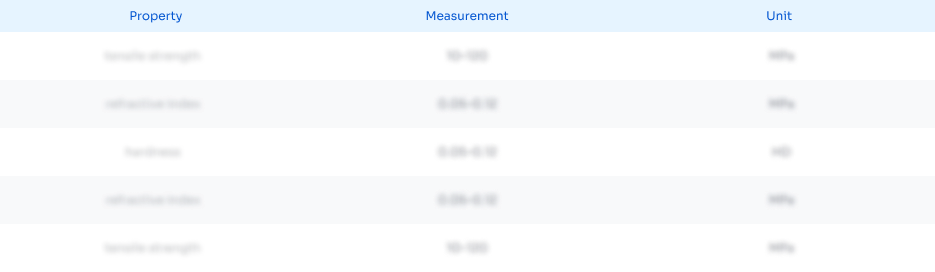
Abstract
Description
Claims
Application Information

- Generate Ideas
- Intellectual Property
- Life Sciences
- Materials
- Tech Scout
- Unparalleled Data Quality
- Higher Quality Content
- 60% Fewer Hallucinations
Browse by: Latest US Patents, China's latest patents, Technical Efficacy Thesaurus, Application Domain, Technology Topic, Popular Technical Reports.
© 2025 PatSnap. All rights reserved.Legal|Privacy policy|Modern Slavery Act Transparency Statement|Sitemap|About US| Contact US: help@patsnap.com