Working method of milling machine clamp
A working method and milling machine fixture technology, applied in the direction of clamping, manufacturing tools, metal processing equipment, etc., can solve the problems of reducing work efficiency and high labor intensity of workers, so as to improve production efficiency, reduce labor intensity of workers, and have a wide range of applications Effect
- Summary
- Abstract
- Description
- Claims
- Application Information
AI Technical Summary
Problems solved by technology
Method used
Image
Examples
Embodiment
[0021] The working method of a milling machine fixture of the present invention, such as figure 1 with figure 2 As shown, including the following steps:
[0022] 1) The control module sends an instruction to run the steering drive system, drives the middle turntable 4 to turn, drives the crimping piece 7 to move to the loading and unloading station, the steering drive system stops, and the crimping piece 7 is kept at the loading and unloading station;
[0023] 2) Replace the workpiece: Take down the processed workpiece, and install a new set of workpieces on the support 3;
[0024] 3) The control module issues a command to make the steering drive system run in the reverse direction, drive the intermediate turntable 4 to turn, drive the crimping piece 7 back to the crimping station, the steering drive system stops, and the crimping piece 7 is kept at the crimping station;
[0025] 4) The control module issues an instruction to run the lifting drive system, drives the adjusting pressur...
PUM
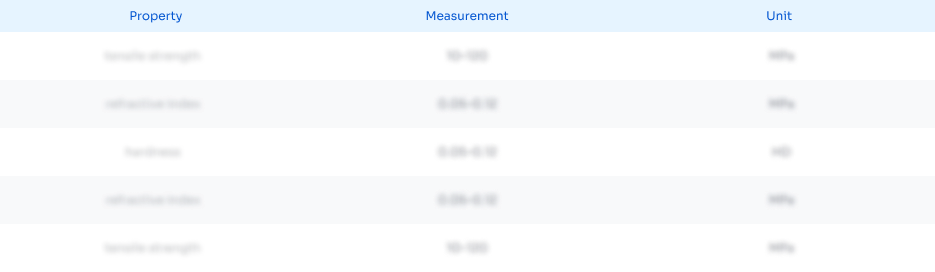
Abstract
Description
Claims
Application Information

- R&D
- Intellectual Property
- Life Sciences
- Materials
- Tech Scout
- Unparalleled Data Quality
- Higher Quality Content
- 60% Fewer Hallucinations
Browse by: Latest US Patents, China's latest patents, Technical Efficacy Thesaurus, Application Domain, Technology Topic, Popular Technical Reports.
© 2025 PatSnap. All rights reserved.Legal|Privacy policy|Modern Slavery Act Transparency Statement|Sitemap|About US| Contact US: help@patsnap.com