Optimization design method for Whiffletree support point position of primary mirror and sub-mirror models of telescope
A technology for optimizing design and support points, applied in the fields of astronomy and mechanical automation, it can solve problems such as affecting imaging quality, time-consuming and labor-intensive, and achieve the effect of plane simplification, reasonable support scheme, and convenient optimization steps.
- Summary
- Abstract
- Description
- Claims
- Application Information
AI Technical Summary
Problems solved by technology
Method used
Image
Examples
Embodiment 1
[0041] Combine the following Figure 1 to Figure 7 The present invention is described further.
[0042] (1) The simplification process of the sub-mirror model. The upper and lower surfaces of the sub-mirror are simplified to obtain a simplified plane model corresponding to the upper and lower surfaces of the sub-mirror. combine figure 2 , figure 2 Midpoint 1 and point 2 are points on the quadratic surface of the upper surface of the sub-mirror and a point on the tangent plane at the center of the sub-mirror, respectively. The axial displacement of point 1 on the curved surface can be reflected by the axial displacement of point 2. The deformation displacement on the subsurface is equivalent to the deformation displacement of the tangent plane at the center point of the analytical sub-mirror surface. For the lower surface, only support points can be considered. Finally, the simplification of the upper and lower surfaces of the sub-mirror from a quadric surface to a plane...
PUM
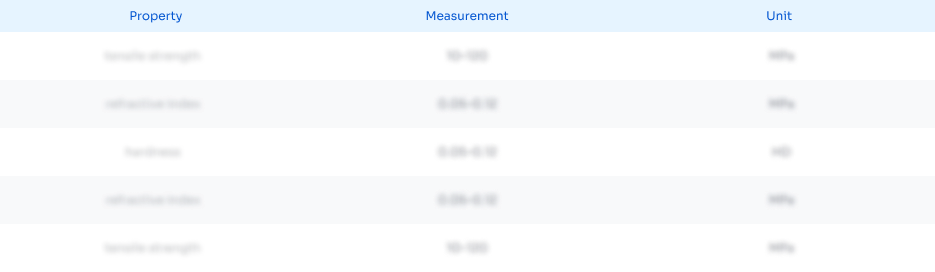
Abstract
Description
Claims
Application Information

- Generate Ideas
- Intellectual Property
- Life Sciences
- Materials
- Tech Scout
- Unparalleled Data Quality
- Higher Quality Content
- 60% Fewer Hallucinations
Browse by: Latest US Patents, China's latest patents, Technical Efficacy Thesaurus, Application Domain, Technology Topic, Popular Technical Reports.
© 2025 PatSnap. All rights reserved.Legal|Privacy policy|Modern Slavery Act Transparency Statement|Sitemap|About US| Contact US: help@patsnap.com