Preparation method of polyacrylonitrile-based high-strength high-modulus carbon fibers
A high-modulus carbon fiber, polyacrylonitrile-based technology, applied in the chemical characteristics of fibers, textiles and papermaking, etc., can solve the problems of simultaneous change, increase, and inability to match the related models of T series carbon fibers, and achieves lower processing temperature and higher tensile strength. The effect of stretching efficiency and easy operation
- Summary
- Abstract
- Description
- Claims
- Application Information
AI Technical Summary
Problems solved by technology
Method used
Image
Examples
Embodiment 1
[0032] (1) Pre-oxidation of PAN precursor
[0033] The 1K low-denier laboratory wet-process self-made PAN precursor was pre-oxidized in an air atmosphere using a gradient temperature rise method. The pre-oxidation start temperature was 210°C, the pre-oxidation end temperature was 255°C, and the pre-oxidation time was 45 minutes.
[0034] (2) Low temperature carbonization
[0035] Put the obtained pre-oxidized fiber into a low-temperature carbonization furnace for low-temperature carbonization treatment, using nitrogen as a protective gas, and the oxygen content in nitrogen is 1.0ppm. The low-temperature carbonization temperature is 700°C, and the low-carbon carbonization time is 3 minutes.
[0036] (3) High temperature carbonization
[0037] Put the obtained low-temperature carbonized fiber into a high-temperature carbonization furnace for high-temperature carbonization treatment, using high-purity nitrogen as a protective gas, and the oxygen content in nitrogen is 1.0ppm. Th...
Embodiment 2
[0042] (1) Pre-oxidation of PAN precursor
[0043] The Weihai extension 6K wet-process PAN precursor was pre-oxidized in an air atmosphere using a gradient heating method. The pre-oxidation start temperature was 200°C, the pre-oxidation termination temperature was 260°C, and the pre-oxidation time was 45 minutes.
[0044] (2) Low temperature carbonization
[0045] The obtained pre-oxidized fiber enters a low-temperature carbonization furnace for low-temperature carbonization treatment, using nitrogen as a protective gas, and the oxygen content in the nitrogen is 1.0 ppm. The low-temperature carbonization temperature is 750°C, and the low-carbon carbonization time is 3 minutes.
[0046] (3) High temperature carbonization
[0047] The fibers enter the high-temperature carbonization furnace after low-temperature carbonization, and high-purity nitrogen is used as the protective gas, and the oxygen content in nitrogen is 1.0ppm. The carbonization temperature is 1600°C, the carbo...
Embodiment 3
[0051] (1) Pre-oxidation of PAN precursor, (2) Low temperature carbonization
[0052] Same as Example 2
[0053] (3) High temperature carbonization
[0054] The obtained low-temperature carbonized fiber enters a high-temperature carbonization furnace for high-temperature carbonization, using high-purity nitrogen as a protective gas, and the oxygen content in the nitrogen is 1.0 ppm. The high-temperature carbonization temperature is 1650° C., the residence time is 2 minutes, and a relative stretching ratio of 96.8% is applied to both ends of the fiber during high-temperature carbonization treatment. The orientation angle of carbon crystallites in the obtained high-temperature carbonized fiber is 17.03°.
[0055] (4) High temperature graphitization
[0056] The obtained high-temperature carbonized fiber enters a graphitization furnace for high-temperature graphitization treatment, and nitrogen gas is used as a protective gas, and the oxygen content in the nitrogen gas is 1.0 ...
PUM
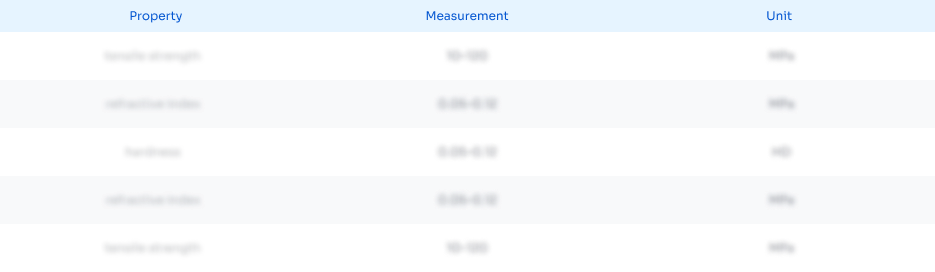
Abstract
Description
Claims
Application Information

- Generate Ideas
- Intellectual Property
- Life Sciences
- Materials
- Tech Scout
- Unparalleled Data Quality
- Higher Quality Content
- 60% Fewer Hallucinations
Browse by: Latest US Patents, China's latest patents, Technical Efficacy Thesaurus, Application Domain, Technology Topic, Popular Technical Reports.
© 2025 PatSnap. All rights reserved.Legal|Privacy policy|Modern Slavery Act Transparency Statement|Sitemap|About US| Contact US: help@patsnap.com