Manufacturing process of blade parts
A manufacturing process and component technology, which is applied to household components, other household appliances, household appliances, etc., can solve the problems of long process time, difficulty in controlling the amount of dipping, and cumbersome manufacturing processes, so as to reduce energy consumption and overcome glue. The effect of surplus quantity and saving manufacturing time
- Summary
- Abstract
- Description
- Claims
- Application Information
AI Technical Summary
Problems solved by technology
Method used
Image
Examples
Embodiment Construction
[0020] In order to enable those skilled in the art to better understand the present invention, specific embodiments of the present invention will be described in detail below in conjunction with the accompanying drawings.
[0021] refer to figure 1 and figure 2 , figure 1 is a schematic diagram of a girder layup according to an embodiment of the present invention, figure 2 is a flowchart of a blade part manufacturing process according to an embodiment of the present invention. An embodiment according to the present invention provides a manufacturing process of a blade component. The blade component may be a main beam of the blade, or a component at another position. In the following description, the main beam will be used as an example for illustration.
[0022] When the main girder is manufactured, it can be carried out on a separate special mold, and then the formed main girder is laid on the blade shell to complete the manufacture of the blade shell. Alternatively, wh...
PUM
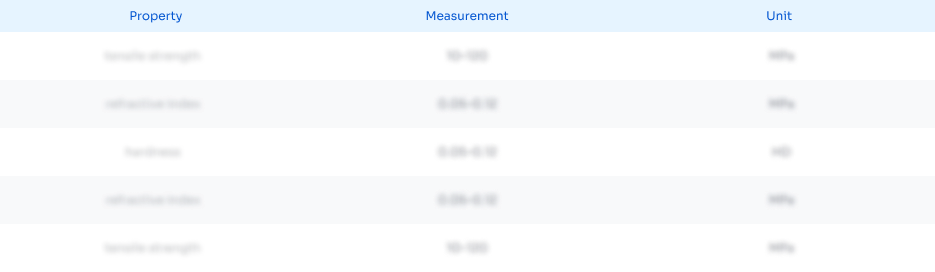
Abstract
Description
Claims
Application Information

- R&D
- Intellectual Property
- Life Sciences
- Materials
- Tech Scout
- Unparalleled Data Quality
- Higher Quality Content
- 60% Fewer Hallucinations
Browse by: Latest US Patents, China's latest patents, Technical Efficacy Thesaurus, Application Domain, Technology Topic, Popular Technical Reports.
© 2025 PatSnap. All rights reserved.Legal|Privacy policy|Modern Slavery Act Transparency Statement|Sitemap|About US| Contact US: help@patsnap.com