Robot joint rotating device directly driven by frameless type permanent magnet synchronous motor
A technology of permanent magnet synchronous motors and robot joints, which is applied in the direction of electromechanical devices, manipulators, electrical components, etc., can solve problems such as bloated robot joints, achieve simplified driving methods and equipment structures, reduce volume, and meet flexible selection requirements Effect
- Summary
- Abstract
- Description
- Claims
- Application Information
AI Technical Summary
Problems solved by technology
Method used
Image
Examples
Embodiment 1
[0029] Such as Figure 1-5 As shown, a frameless permanent magnet synchronous motor direct-driven robot joint rotation device, the robot joint rotation device includes a forearm 1, a rotating shaft 3 and a rear arm 2; the end of the forearm 1 is provided with a mounting hole 11; The rotating shaft 3 is installed in the mounting hole 11 through the bearing 6; the rear arm 2 is connected with the rotating shaft 3, and rotates around the forearm 1 through the rotating shaft 3; the rotating shaft 3 is made of frameless The permanent magnet synchronous motor is directly driven; the frameless permanent magnet synchronous motor includes a stator assembly 7 and a rotor assembly 8; the stator assembly 7 is fixed on the base of the forearm 1 to provide a rotating magnetic field for the rotor assembly 8; it has a permanent magnet The characteristic rotor assembly 8 is fixedly mounted on the rotating shaft 3;
[0030] Wherein, the stator assembly 7 includes a stator core 1 72 and a stato...
Embodiment 2
[0034] Such as Figure 6-8As shown, a frameless permanent magnet synchronous motor direct-driven robot joint rotation device, the robot joint rotation device includes a forearm 1, a rotating shaft 3 and a rear arm 2; the end of the forearm 1 is provided with a mounting hole 11; The rotating shaft 3 is installed in the mounting hole 11 through the bearing 6; the rear arm 2 is connected with the rotating shaft 3, and rotates around the forearm 1 through the rotating shaft 3; the rotating shaft 3 is made of frameless The permanent magnet synchronous motor is directly driven; the frameless permanent magnet synchronous motor includes a stator assembly 7 and a rotor assembly 8; the stator assembly 7 is fixed on the base of the forearm 1 to provide a rotating magnetic field for the rotor assembly 8; it has a permanent magnet The characteristic rotor assembly 8 is fixedly mounted on the rotating shaft 3;
[0035] Wherein, the stator assembly 7 includes a second stator core 73 and a s...
Embodiment 3
[0039] Such as Figure 9 As shown, a frameless permanent magnet synchronous motor direct-driven robot joint rotation device, the robot joint rotation device includes a forearm 1, a rotating shaft 3 and a rear arm 2; the end of the forearm 1 is provided with a mounting hole 11; The rotating shaft 3 is installed in the mounting hole 11 through the bearing 6; the rear arm 2 is connected with the rotating shaft 3, and rotates around the forearm 1 through the rotating shaft 3; the rotating shaft 3 is made of frameless The permanent magnet synchronous motor is directly driven; the frameless permanent magnet synchronous motor includes a stator assembly 7 and a rotor assembly 8; the stator assembly 7 is fixed on the base of the forearm 1 to provide a rotating magnetic field for the rotor assembly 8; it has a permanent magnet The characteristic rotor assembly 8 is fixedly mounted on the rotating shaft 3;
[0040] Wherein, the stator assembly 7 includes stator core 1 72 and stator core...
PUM
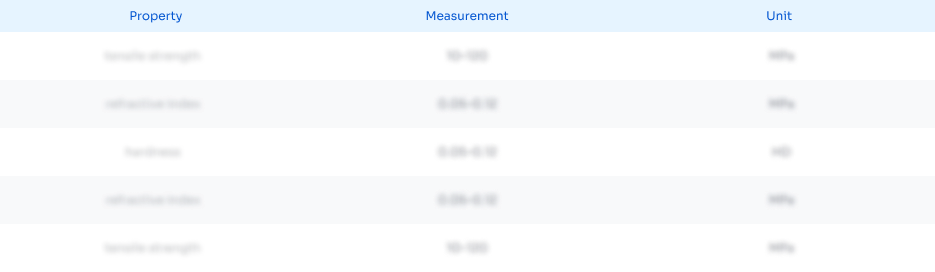
Abstract
Description
Claims
Application Information

- R&D Engineer
- R&D Manager
- IP Professional
- Industry Leading Data Capabilities
- Powerful AI technology
- Patent DNA Extraction
Browse by: Latest US Patents, China's latest patents, Technical Efficacy Thesaurus, Application Domain, Technology Topic, Popular Technical Reports.
© 2024 PatSnap. All rights reserved.Legal|Privacy policy|Modern Slavery Act Transparency Statement|Sitemap|About US| Contact US: help@patsnap.com