A method for setting process lubrication system for single-stand reversing rolling mill in cold rolling
A technology of process lubrication and setting method, applied in the field of cold rolling, can solve the problems of rolling force difference, large thickness difference control fluctuation, etc., and achieve small rolling force deviation, reduced thickness fluctuation, and rolling force deviation. changing effect
- Summary
- Abstract
- Description
- Claims
- Application Information
AI Technical Summary
Problems solved by technology
Method used
Image
Examples
Embodiment Construction
[0054] The present invention will be described in further detail below in conjunction with the accompanying drawings and specific embodiments.
[0055] The present invention proposes a process lubrication system setting method suitable for cold-rolled single-stand reversible rolling mills. The number of stand rolls in the cold-rolled single-stand reversible rolling mill can be 4 rolls, 6 rolls, 12 rolls, 18 rolls or 20 rolls. roll. The process lubrication of the cold-rolled single-stand reversing rolling mill of the present invention adopts such as figure 2 In the shown structure, the emulsion injection mechanism 7 is equipped at the roll gap of the single-stand reversing rolling mill in cold rolling. In other embodiments, emulsion injection beam devices 3 can also be added on both sides of the rolling mill. The emulsion is cold During rolling production, a small amount of rolling oil and a large amount of water are mixed through a stirring device; the concentration, tempera...
PUM
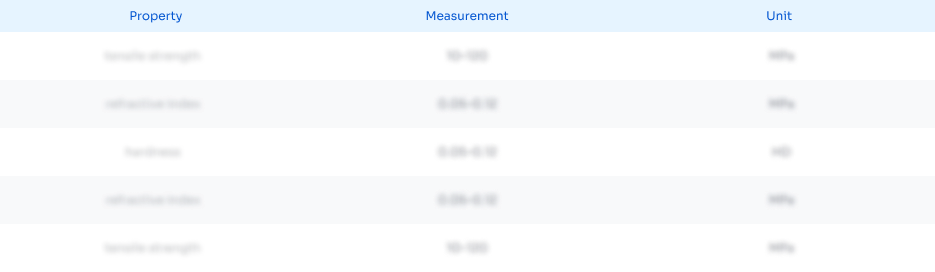
Abstract
Description
Claims
Application Information

- Generate Ideas
- Intellectual Property
- Life Sciences
- Materials
- Tech Scout
- Unparalleled Data Quality
- Higher Quality Content
- 60% Fewer Hallucinations
Browse by: Latest US Patents, China's latest patents, Technical Efficacy Thesaurus, Application Domain, Technology Topic, Popular Technical Reports.
© 2025 PatSnap. All rights reserved.Legal|Privacy policy|Modern Slavery Act Transparency Statement|Sitemap|About US| Contact US: help@patsnap.com