Adaptive underactuated robotic gripper
An adaptive and robotic technology, applied in the field of robot grippers, can solve problems such as complex mechanical structure and control system, increased degrees of freedom and drives, and reduced grasping force, achieving compact structure, large grasping range, and powerful effect
- Summary
- Abstract
- Description
- Claims
- Application Information
AI Technical Summary
Problems solved by technology
Method used
Image
Examples
Embodiment Construction
[0052] In order to describe the present invention more clearly, the present invention will be further elaborated below in conjunction with the accompanying drawings and specific embodiments. What is illustrated here is that the exemplary embodiment of the present invention is a two-finger robot gripper, but the present invention is not limited to two Finger robot grippers also include other similar multi-finger robot grippers, as long as the working methods and principles disclosed in the present invention are used, they all belong to the protection scope of the present invention.
[0053] see figure 1 and figure 2, the invention discloses an adaptive underactuated robot gripper, comprising a gripper housing 1, a drive module 2 and a finger module 3; the gripper housing 1 includes a gripper front case 4, a gripper rear case 5 and The fixed flange 6, the jaw front shell 4 is connected with the jaw rear shell 5, and is connected with the fixed flange 6 by bolts; the driving mo...
PUM
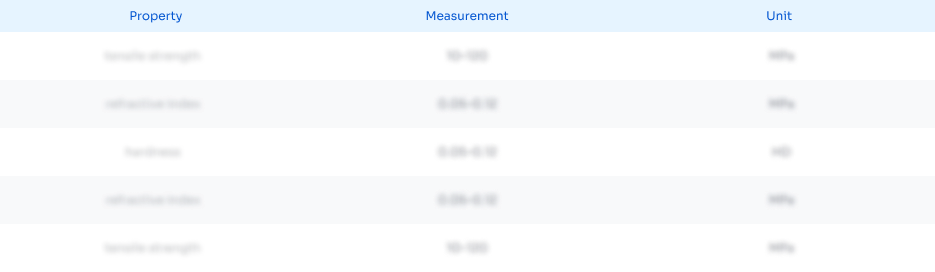
Abstract
Description
Claims
Application Information

- R&D Engineer
- R&D Manager
- IP Professional
- Industry Leading Data Capabilities
- Powerful AI technology
- Patent DNA Extraction
Browse by: Latest US Patents, China's latest patents, Technical Efficacy Thesaurus, Application Domain, Technology Topic, Popular Technical Reports.
© 2024 PatSnap. All rights reserved.Legal|Privacy policy|Modern Slavery Act Transparency Statement|Sitemap|About US| Contact US: help@patsnap.com