Intelligent yarn discharging and rectangular coordinate robot automatic yarn supplementing system
A Cartesian coordinate and robot technology, applied in the direction of conveying filamentous materials, thin material processing, transportation and packaging, etc., can solve the problems affecting the quality of yarn rolls, high labor intensity, difficult yarn repairing operations, etc., to improve yarn unloading and The effect of filling yarn efficiency, reducing labor intensity and avoiding manual handling
- Summary
- Abstract
- Description
- Claims
- Application Information
AI Technical Summary
Problems solved by technology
Method used
Image
Examples
Embodiment Construction
[0022] The present invention will be further described below in conjunction with the accompanying drawings and examples, but the present invention is not limited in any way. Any changes or improvements made based on the teaching of the present invention belong to the protection scope of the present invention.
[0023] like Figures 1 to 8 As shown, the present invention includes a yarn unloading support 1, a yarn unloading mechanism 2, a horizontal driving device for unloading yarn 3, a yarn storage rack 4, a yarn storage tank 5, a yarn repairing support 6, an X-axis beam 7, a Z-axis vertical shaft 8, and a Y-axis Longitudinal beam 9, A-axis mounting seat 10, clamp 11, clamp rotation driving device 12, the yarn unloading mechanism 2 is vertically arranged on one or both sides of the yarn unloading support 1, and the two ends of the yarn unloading horizontal driving device 3 are respectively It is fixedly connected or hinged with the yarn unloading support 1 and the yarn unload...
PUM
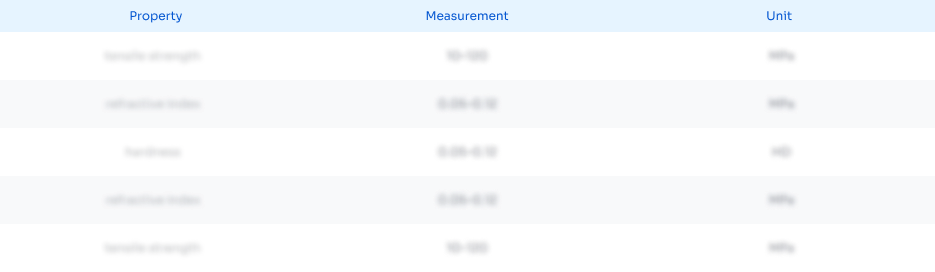
Abstract
Description
Claims
Application Information

- R&D
- Intellectual Property
- Life Sciences
- Materials
- Tech Scout
- Unparalleled Data Quality
- Higher Quality Content
- 60% Fewer Hallucinations
Browse by: Latest US Patents, China's latest patents, Technical Efficacy Thesaurus, Application Domain, Technology Topic, Popular Technical Reports.
© 2025 PatSnap. All rights reserved.Legal|Privacy policy|Modern Slavery Act Transparency Statement|Sitemap|About US| Contact US: help@patsnap.com