Electromechanical integrated low-frequency acoustic emission energy transducer
An integrated, acoustic emission technology, applied in the direction of ultrasonic/sonic/infrasonic generation, etc., can solve the problems of affecting the strength of the piston, insufficient rigidity, inconvenient installation and use, etc., to meet the acoustic transmission characteristic test, compact structure, simple structure Effect
- Summary
- Abstract
- Description
- Claims
- Application Information
AI Technical Summary
Problems solved by technology
Method used
Image
Examples
Embodiment Construction
[0026] Specific embodiments of the present invention will be described below.
[0027] Such as figure 1 As shown, the electromechanical integrated low-frequency acoustic emission transducer is connected by an electromagnetic drive device 1, a low-frequency acoustic excitation device 2 for balancing the static pressure of the liquid medium in the tube, and an acoustic measurement chamber to form an integrated structure;
[0028] The concrete structure of electromagnetic drive device 1 is as follows:
[0029] Comprising the magnetic cylinder back cover 14, the upper and lower sides of the magnetic cylinder back cover 14 are respectively provided with fixed magnetic cylinders 22, fixed magnets 16 are arranged on the surface of the fixed magnetic cylinder 22, and movable magnets 16 are arranged between two adjacent fixed magnets 16 up and down. The movable magnetic cylinder 11 is provided with a connecting damper 12 inside the movable magnetic cylinder 11 . One end of each fixed...
PUM
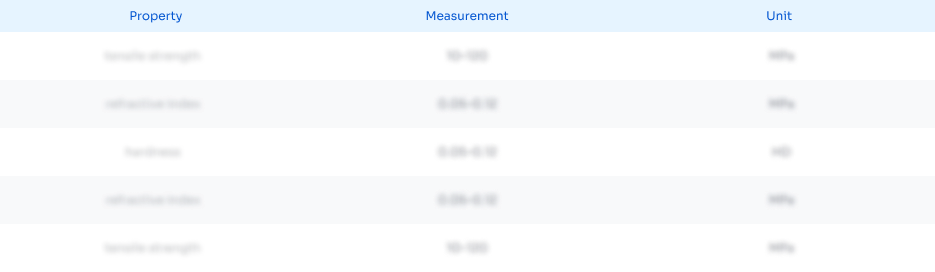
Abstract
Description
Claims
Application Information

- R&D
- Intellectual Property
- Life Sciences
- Materials
- Tech Scout
- Unparalleled Data Quality
- Higher Quality Content
- 60% Fewer Hallucinations
Browse by: Latest US Patents, China's latest patents, Technical Efficacy Thesaurus, Application Domain, Technology Topic, Popular Technical Reports.
© 2025 PatSnap. All rights reserved.Legal|Privacy policy|Modern Slavery Act Transparency Statement|Sitemap|About US| Contact US: help@patsnap.com