A Design Method for Complex Shell Based on 3D Printing
A technology of three-dimensional printing and design method, which is applied in the field of hydraulic machinery, can solve problems such as time-consuming and affecting the progress of model development, and achieve the effect of oil circuit optimization
- Summary
- Abstract
- Description
- Claims
- Application Information
AI Technical Summary
Problems solved by technology
Method used
Image
Examples
Embodiment Construction
[0040] The present invention will be further described below in conjunction with specific drawings and embodiments. Such as Figure 1-13 as shown,
[0041] The present invention provides a complex shell design method based on three-dimensional printing, comprising the following steps:
[0042] 1) Blank design of components with equal wall thickness: According to the selected shell material properties and load conditions, the calculation formula of tensile strength is used to calculate the wall thickness h of the component hole; the three-dimensional structure of the component hole completed by the component designer according to the functional performance requirements of the component Based on the model, in UGS NX software or other 3D structural modeling software, use the related tools of "model enlargement" or "sketch offset curve", and use the calculated wall thickness value h as the enlargement (offset) parameter to complete the component The three-dimensional structural ...
PUM
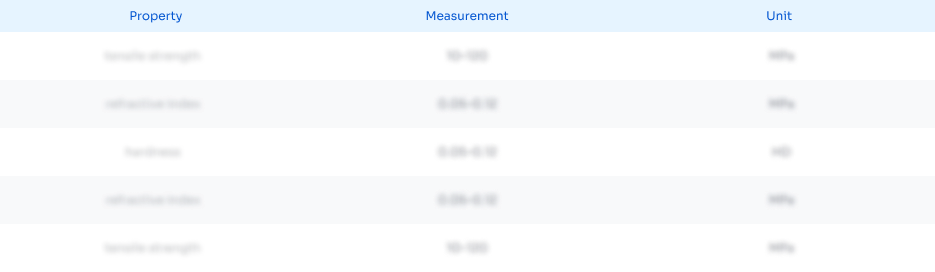
Abstract
Description
Claims
Application Information

- Generate Ideas
- Intellectual Property
- Life Sciences
- Materials
- Tech Scout
- Unparalleled Data Quality
- Higher Quality Content
- 60% Fewer Hallucinations
Browse by: Latest US Patents, China's latest patents, Technical Efficacy Thesaurus, Application Domain, Technology Topic, Popular Technical Reports.
© 2025 PatSnap. All rights reserved.Legal|Privacy policy|Modern Slavery Act Transparency Statement|Sitemap|About US| Contact US: help@patsnap.com