Technique for promoting dye permeability and depth of active dye
A reactive dye and process technology, applied in the field of textile printing and dyeing, can solve the problems of whitening, poor dye penetration, affecting product quality, etc., and achieve the effects of increasing penetration time, dyeing depth, and improving permeability.
- Summary
- Abstract
- Description
- Claims
- Application Information
AI Technical Summary
Problems solved by technology
Method used
Examples
Embodiment 1
[0021] Fabric: weave specification CM100 / 3*FFT20(105D)*146*70*55 / 56 deep black;
[0022] The dyeing process is as follows: pre-treatment of fabrics → padding dye solution → stacking → first drying → padding color fixing solution → steaming → high temperature soaping → second drying → finishing.
[0023] The padding dyeing solution is carried out on the Benninger uniform padding machine, the padding reactive dyeing solution, the dye combination is BKC-G (Huntsman) 66.3g / L, RS-B (Huntsman) 15.2g / L, NC-R ( Huntsman) 2.6g / L, anti-swimming agent 20g / L, penetrant MRZ (Archroma) 3g / L, vehicle speed 40m / min, cold pile coiling tension 100N.
[0024] 1. Stacking: The stacking temperature is 25°C, and the stacking time is 10 hours.
[0025] 2. The first drying: drying in Monforts Thermex 6500 continuous dyeing machine, speed 40m / min, infrared pre-drying 700°C, drying room temperature 130°C, circulating air volume 60%, exhaust air 60%, no air Rolling cars and troughs.
[0026] 3. Paddi...
Embodiment 2
[0039] Fabric: weave specification CPT140 / 2*CPT140 / 2*190*100*57 / 58 navy blue.
[0040] The dyeing process is as follows: pre-treatment of fabrics → padding dye solution → stacking → first drying → padding color fixing solution → steaming → high temperature soaping → second drying → finishing.
[0041] 1. The padding dyeing solution is carried out on a Benninger uniform padding machine, and the padding reactive dyeing solution is dyed. The dye combination is NC-R (Huntsman) 51.2g / L, BCA (Archroma) 14.5g / L, RHF-3B ( Archroma) 7.8g / L, anti-swimming agent 10g / L, penetrating agent MRZ (Archroma) 2g / L, vehicle speed 50m / min, cold stack winding tension 70N.
[0042] 2. Stacking: The stacking temperature is 25°C, and the stacking time is 4 hours.
[0043] 3. The first drying: drying in Monforts Thermex 6500 continuous dyeing machine, speed 50m / min, infrared pre-drying 650°C, drying room temperature 110°C, circulating air volume 50%, exhaust air 50%, not leaving Rolling cars and trou...
PUM
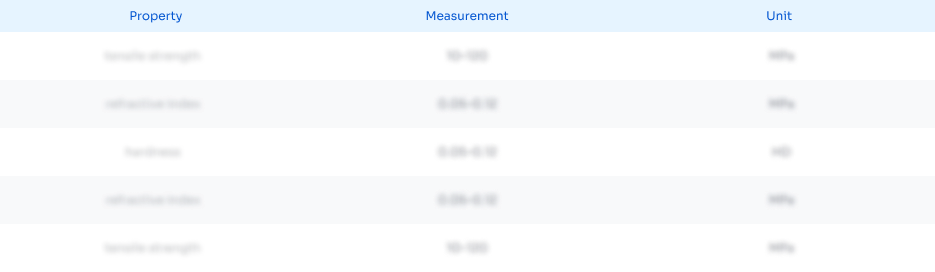
Abstract
Description
Claims
Application Information

- R&D
- Intellectual Property
- Life Sciences
- Materials
- Tech Scout
- Unparalleled Data Quality
- Higher Quality Content
- 60% Fewer Hallucinations
Browse by: Latest US Patents, China's latest patents, Technical Efficacy Thesaurus, Application Domain, Technology Topic, Popular Technical Reports.
© 2025 PatSnap. All rights reserved.Legal|Privacy policy|Modern Slavery Act Transparency Statement|Sitemap|About US| Contact US: help@patsnap.com