A Method for Automatic Correction of Initial Wavelength of Optical Fiber Sensor
A fiber optic sensor and sensor technology, applied in the direction of converting sensor output, using optical devices to transmit sensing components, instruments, etc., can solve problems such as the inability to accurately and effectively capture bridge structural health and safety information, hidden safety hazards, and abnormal monitoring data
- Summary
- Abstract
- Description
- Claims
- Application Information
AI Technical Summary
Problems solved by technology
Method used
Image
Examples
Embodiment Construction
[0018] The present invention will be further described in detail below in conjunction with the accompanying drawings and specific embodiments.
[0019] figure 1 A method for automatically correcting the initial wavelength of an optical fiber sensor is shown, and its specific steps are:
[0020] Step S1, select the bridge to be monitored, analyze its structure, and determine the monitoring items;
[0021] Step S2, select the corresponding optical fiber sensor according to the monitoring item, select the parameters of the optical fiber sensor and design the layout, and install the optical fiber sensor at the corresponding measuring point position;
[0022] Step S3, collect the strain, deformation and displacement signals of the bridge structure through the fiber optic sensor, and then convert the signal collected by the fiber optic sensor into real-time wavelength data through the fiber grating demodulator;
[0023] Step S4. Select the wavelength data from 1:00 to 4:00 in the ...
PUM
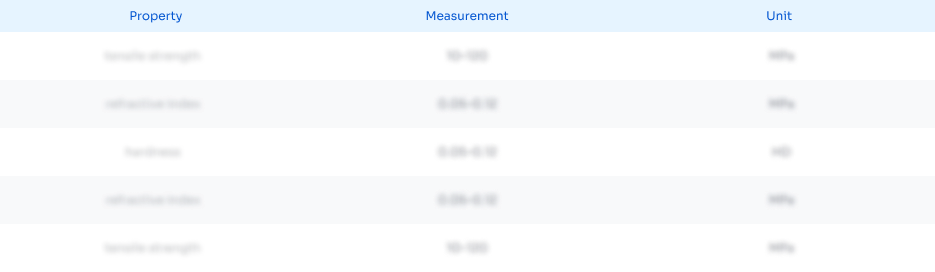
Abstract
Description
Claims
Application Information

- Generate Ideas
- Intellectual Property
- Life Sciences
- Materials
- Tech Scout
- Unparalleled Data Quality
- Higher Quality Content
- 60% Fewer Hallucinations
Browse by: Latest US Patents, China's latest patents, Technical Efficacy Thesaurus, Application Domain, Technology Topic, Popular Technical Reports.
© 2025 PatSnap. All rights reserved.Legal|Privacy policy|Modern Slavery Act Transparency Statement|Sitemap|About US| Contact US: help@patsnap.com