an isolation mechanism
A technology of isolating mechanism and rotating motor, applied in the testing of machine/structural components, mechanical equipment, machine/engine, etc., can solve the problem of large change in driving force, difficulty in realizing the action performance of the gunpowder pin puller, and inability to realize the reverse rotation of the rotating wheel. Turn drive and other problems to achieve the effect of improving reliability
- Summary
- Abstract
- Description
- Claims
- Application Information
AI Technical Summary
Problems solved by technology
Method used
Image
Examples
Embodiment Construction
[0022] The technical solution of the present invention is further described below, but the scope of protection is not limited to the description.
[0023] Such as figure 1 , figure 2 The shown isolation mechanism includes a rotating shaft 3, a powder column 4, a rotating wheel 5, a mounting seat 6, an action source 8, and a rotating motor 9; the mounting seat 6 has a cylindrical cavity, and the rotating shaft 3 is fixed vertically and coaxially In the cavity, a rotating wheel 5 is fixed on the rotating shaft 3, a rotating motor 9 is fixed at the bottom of the rotating shaft 3, and the rotating motor 9 drives the rotating shaft 3 to rotate; the inner edge of the rotating wheel 5 is fixed with a drug column 4 and a mounting seat 6 The action source 8 is set at the position below the corresponding powder column 4 inside.
[0024] An electromagnetic clamp 7 is sleeved and fixed on the rotating shaft 3 between the rotating wheel 5 and the rotating motor 9 .
[0025] An openable...
PUM
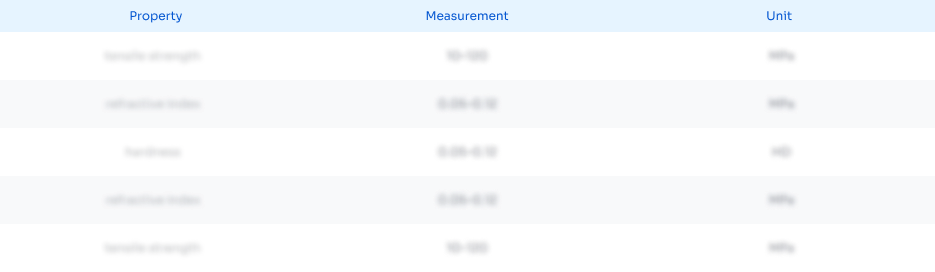
Abstract
Description
Claims
Application Information

- R&D
- Intellectual Property
- Life Sciences
- Materials
- Tech Scout
- Unparalleled Data Quality
- Higher Quality Content
- 60% Fewer Hallucinations
Browse by: Latest US Patents, China's latest patents, Technical Efficacy Thesaurus, Application Domain, Technology Topic, Popular Technical Reports.
© 2025 PatSnap. All rights reserved.Legal|Privacy policy|Modern Slavery Act Transparency Statement|Sitemap|About US| Contact US: help@patsnap.com