Multi-drive safe lifting elevator
A safe lifting and multi-drive technology, which is applied in elevators, elevators in buildings, transportation and packaging, etc., can solve the problems of slipping, falling, broken rope, rushing to the top, squatting at the bottom, low space utilization of the well, and civil engineering coordination Large projects and other problems, to achieve the effect of improving the space utilization of the hoistway, reducing the capacity requirements of the power grid, and reducing the starting current
- Summary
- Abstract
- Description
- Claims
- Application Information
AI Technical Summary
Problems solved by technology
Method used
Image
Examples
Embodiment Construction
[0034] Now the present invention is further described in conjunction with description of drawings and embodiments:
[0035] refer to Figure 1 to Figure 3 , a multi-drive safety lift, comprising a guide rail assembly 1, a car assembly 2 running on the guide rail assembly 1, a first power output module 3 driving the car assembly 2 to run on the guide rail assembly 1, the first power The output module 3 includes an active power output drive and a ball screw 4, wherein:
[0036] Also includes a second power output module 5, the second power output module 5 is arranged on the top of the ball screw, the second power output module 5 includes,
[0037] A servo motor 51 is fixed on the motor mounting plate 54 for power output;
[0038] A shaft coupling 53 installed on the output shaft of the servo motor 51 for power transmission;
[0039] A two-way overrunning clutch 52 is flange-connected to the bearing seat 41 on the top of the ball screw 4, wherein one end is connected to the sh...
PUM
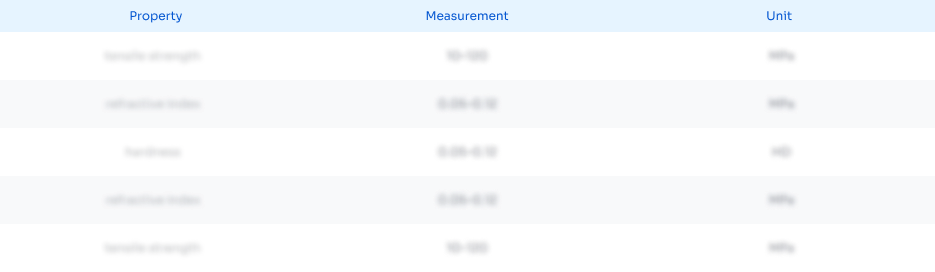
Abstract
Description
Claims
Application Information

- R&D Engineer
- R&D Manager
- IP Professional
- Industry Leading Data Capabilities
- Powerful AI technology
- Patent DNA Extraction
Browse by: Latest US Patents, China's latest patents, Technical Efficacy Thesaurus, Application Domain, Technology Topic, Popular Technical Reports.
© 2024 PatSnap. All rights reserved.Legal|Privacy policy|Modern Slavery Act Transparency Statement|Sitemap|About US| Contact US: help@patsnap.com