A Method for Measuring Stiffness Coefficient of Cracked Rotor
A technology of stiffness coefficient and measurement method, which is applied in the field of measurement of the stiffness coefficient of cracked rotors, can solve the problems of difficulty in measuring the stiffness coefficient of the rotor, and it is difficult to paste the crack tip of the strain gauge, so as to avoid singularity problems, low cost and simple method. Effect
- Summary
- Abstract
- Description
- Claims
- Application Information
AI Technical Summary
Problems solved by technology
Method used
Image
Examples
Embodiment Construction
[0039] see figure 1 with figure 2 , the measurement method of cracked rotor stiffness coefficient in this embodiment is:
[0040] On the cracked rotor 1, four axial measurement positions are arranged along the axial direction of the cracked rotor 1, and the four axial measurement positions are distributed in pairs on both sides of the crack 2; Four measuring points are distributed, and strain gauges are pasted on each measuring point, and a total of sixteen strain gauges R are pasted ij, i=1,2,3,4; j=1,2,3,4; among them, R i2 and R i4 is the strain gauge at the i-th axial measurement position and at a pair of measurement points along the direction of the crack opening; R i1 and R i3 is the strain gauge at a pair of measuring points at the i-th axial measuring position, which are also in the direction perpendicular to the crack opening; and R 11 , R 21 , R 31 and R 41 co-located on the same straight line, R 13 , R 23 , R 33 and R 43 co-located on the same straight...
PUM
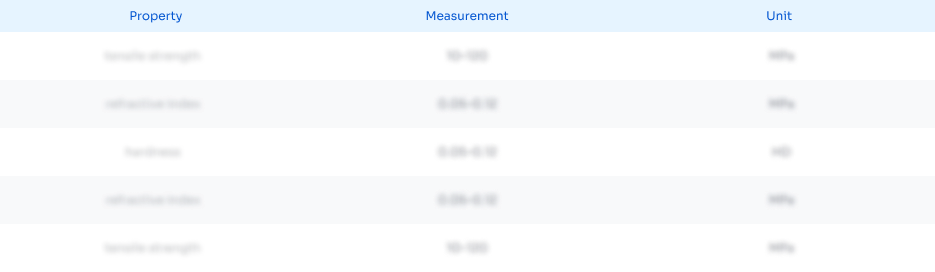
Abstract
Description
Claims
Application Information

- R&D
- Intellectual Property
- Life Sciences
- Materials
- Tech Scout
- Unparalleled Data Quality
- Higher Quality Content
- 60% Fewer Hallucinations
Browse by: Latest US Patents, China's latest patents, Technical Efficacy Thesaurus, Application Domain, Technology Topic, Popular Technical Reports.
© 2025 PatSnap. All rights reserved.Legal|Privacy policy|Modern Slavery Act Transparency Statement|Sitemap|About US| Contact US: help@patsnap.com