A dipping device and method for preparing 3D printing consumables
A dipping device and 3D printing technology, applied in the field of additive manufacturing, can solve the problems of high viscosity of the glue thermoplastic resin, affecting the mechanical strength of the wire, and difficulty in fiber infiltration. Solve the effect of difficult infiltration
- Summary
- Abstract
- Description
- Claims
- Application Information
AI Technical Summary
Problems solved by technology
Method used
Image
Examples
Embodiment Construction
[0035] use figure 1 The impregnation device shown in the figure impregnates fiber yarn bundles, and the number of selected fish-spindle-shaped prepreg rolls is one, the short axis size is 68mm, and the long axis size is 136mm; the die settings are as follows: the diameter of the primary guide die The diameter of the secondary guide die is 18mm, the diameter of the secondary guide die is 4.5mm, and the diameter of the final die is 3mm;
[0036] During the dipping process, the fiber yarn bundles are made of yarn bundles with a forming diameter of 3mm and an unfolded width of 140mm. The dipping solution is made of thermoplastic resin PEEK. Die 380°C, final die 360°C, such as figure 2 As shown in the flowchart, the fiber bundle is preheated through the fiber preheating die, and then dipped along the tension roller, guide roller, fish-spindle-shaped dipping roller, and guide dies at all levels in sequence, and then passed through the final die for shaping. The prepreg bundle is ...
PUM
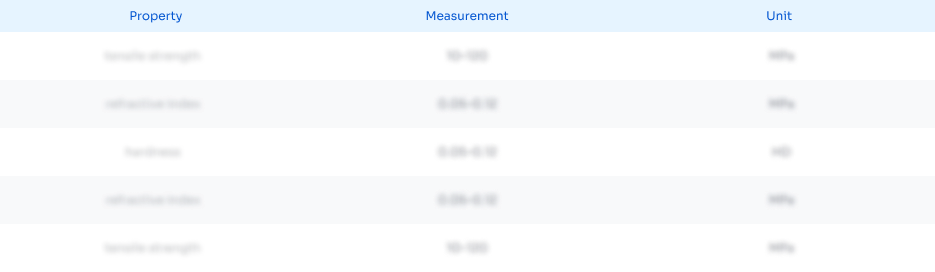
Abstract
Description
Claims
Application Information

- Generate Ideas
- Intellectual Property
- Life Sciences
- Materials
- Tech Scout
- Unparalleled Data Quality
- Higher Quality Content
- 60% Fewer Hallucinations
Browse by: Latest US Patents, China's latest patents, Technical Efficacy Thesaurus, Application Domain, Technology Topic, Popular Technical Reports.
© 2025 PatSnap. All rights reserved.Legal|Privacy policy|Modern Slavery Act Transparency Statement|Sitemap|About US| Contact US: help@patsnap.com