Calibration wafer and method of manufacturing the same
A technology of wafer and deposition method, applied in semiconductor/solid-state device parts, semiconductor/solid-state device testing/measurement, semiconductor devices, etc., can solve the problems of melting point blasting, affecting the measurement accuracy of the machine, and achieve the effect of good thermal conductivity
- Summary
- Abstract
- Description
- Claims
- Application Information
AI Technical Summary
Problems solved by technology
Method used
Image
Examples
Embodiment 1
[0030] figure 2 Shown is a calibration wafer provided by the present invention, the calibration wafer includes a substrate wafer and calibration particles formed on the substrate wafer, the calibration particles are alumina particles, and the alumina particles pass through The deposition method deposits in one half of the surface of the substrate wafer.
[0031] In the first embodiment, the substrate wafer is divided into four scanning areas, which are the first scanning area A, the second scanning area B, the third scanning area C, and the fourth scanning area D. There are five groups of calibration particles in each scanning area.
[0032] Specifically, the substrate wafer is a conventional silicon wafer. Moreover, the shape of the substrate silicon wafer is circular. The first scanning area A, the second scanning area B, the third scanning area C, and the fourth scanning area D are all fan rings with the center of the circular substrate wafer as the center, and the The...
Embodiment 2
[0037] A method for manufacturing a calibration wafer, the schematic flow chart is as image 3 shown, including the following steps:
[0038] Step S31, dissolving alumina particles with the same radius in deionized water to form a solution;
[0039] Step S32, passing dry air into the solution;
[0040] Step S33, depositing the aluminum oxide particles on the substrate wafer by a semi-deposition method.
[0041] Specifically, the alumina particles are prepared by a sol-gel method, and the alumina particles are deposited on half of the surface of the substrate wafer by a semi-deposition method.
[0042] specific, Figure 4 for manufacturing figure 2The equipment for calibrating the wafer shown includes a syringe 41 for containing the solution; an air dryer 42 communicates with the syringe 41 through an air pipe, and feeds dry air into the solution in the syringe 41, and then injects dry air into the liner. While depositing the aluminum oxide particles on the bottom wafer, ...
PUM
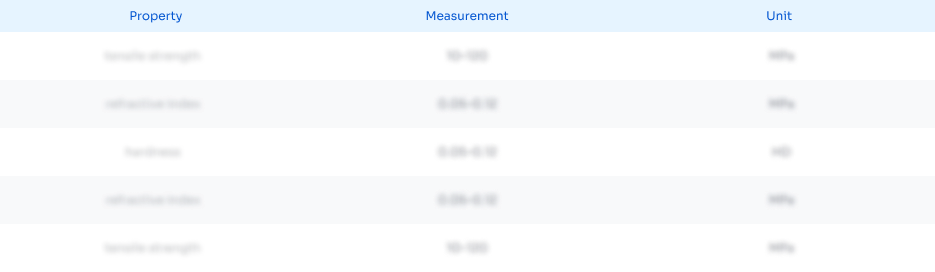
Abstract
Description
Claims
Application Information

- R&D
- Intellectual Property
- Life Sciences
- Materials
- Tech Scout
- Unparalleled Data Quality
- Higher Quality Content
- 60% Fewer Hallucinations
Browse by: Latest US Patents, China's latest patents, Technical Efficacy Thesaurus, Application Domain, Technology Topic, Popular Technical Reports.
© 2025 PatSnap. All rights reserved.Legal|Privacy policy|Modern Slavery Act Transparency Statement|Sitemap|About US| Contact US: help@patsnap.com