Piezoelectric stick-slip micro nano angular displacement platform and driving method thereof
A driving method and angular displacement technology, which is applied in the direction of large fixed members, metal processing machinery parts, metal processing equipment, etc., can solve the problems of large structure size, high production cost, and low positioning accuracy, and achieve lightweight cost and simple assembly , The effect of high positioning accuracy
- Summary
- Abstract
- Description
- Claims
- Application Information
AI Technical Summary
Problems solved by technology
Method used
Image
Examples
specific Embodiment approach 1
[0031] Specific implementation mode one: combine Figure 1~Figure 10 Describe this embodiment. This embodiment provides a specific implementation of an oblique lever amplified piezoelectric stick-slip micro-nano angular displacement stage. The specific implementation is described as follows:
[0032] The oblique lever amplified piezoelectric stick-slip micro-nano angular displacement stage is composed of a sliding table 1, a lateral drive device 2, a baffle 3 and a base 4; the sliding table 1 passes through an arc-shaped dovetail slider 1 -1-4 and the arc-shaped dovetail groove 4-1 are installed on the upper end of the base 4, and the lateral drive device 2 is fixedly installed on the base through the screw connection of the fixing bolt I2-5 and the installation threaded hole II4-3. In the seat 4, the two baffles 3 are respectively fixed and installed on both sides of the base 4 through the screw connection of the fixing bolt II3-2 and the installation threaded hole III4-4. ...
specific Embodiment approach 2
[0037] Specific implementation mode two: combination Figure 11~12 Describe this embodiment. This embodiment provides a specific embodiment of a ladder-shaped lever-amplified piezoelectric stick-slip micro-nano angular displacement stage. The specific structural composition of the lever amplifying mechanism 2-1 is different.
[0038] The lever amplifying mechanism 2-1 utilizes a stepped lever 2-1-9 to amplify displacement, and one side of the lever amplifying mechanism 2-1 is provided with a semicircular flexible hinge 2-1-1 and a connecting rod I2-1- 2. Both ends of the connecting rod I2-1-2 are respectively connected to a semicircular flexible hinge 2-1-1, and the other side of the lever amplification mechanism 2-1 is provided with a circular flexible hinge 2-1-8 and the connecting rod II 2-1-5, the front end of the connecting rod II 2-1-5 is connected to a circular flexible hinge 2-1-8, the semicircular flexible hinge 2-1-1 and the circular flexible hinge 2 -1-8 has fille...
specific Embodiment approach 3
[0039] Specific implementation mode three: combination Figure 13~14 Describe this embodiment. This embodiment provides a specific embodiment of a parallel lever amplified piezoelectric stick-slip micro-nano angular displacement stage. Its structural composition, connection method, and positioning method are the same as those of the first and second embodiments. The difference is that The specific structural composition of its lever amplifying mechanism 2-1 is different.
[0040] The lever amplifying mechanism 2-1 uses parallel levers 2-1-11 to amplify the displacement, and one side of the lever amplifying mechanism 2-1 is provided with a semicircular flexible hinge 2-1-1 and a connecting rod I2-1-2 , the two ends of the connecting rod I2-1-2 are respectively connected to a semicircular flexible hinge 2-1-1, and the other side of the lever amplification mechanism 2-1 is provided with a semicircular flexible hinge 2-1-1 and the connecting rod II 2-1-5, the front end of the con...
PUM
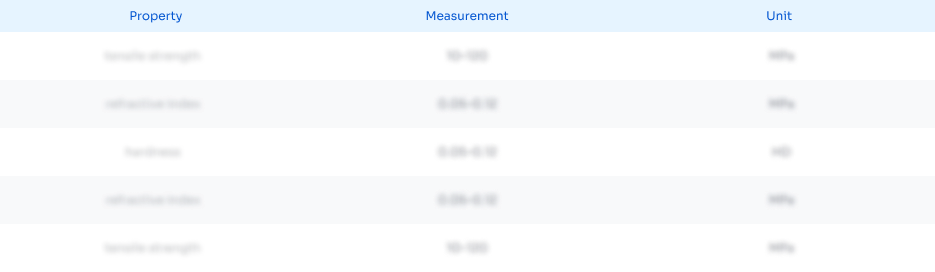
Abstract
Description
Claims
Application Information

- R&D
- Intellectual Property
- Life Sciences
- Materials
- Tech Scout
- Unparalleled Data Quality
- Higher Quality Content
- 60% Fewer Hallucinations
Browse by: Latest US Patents, China's latest patents, Technical Efficacy Thesaurus, Application Domain, Technology Topic, Popular Technical Reports.
© 2025 PatSnap. All rights reserved.Legal|Privacy policy|Modern Slavery Act Transparency Statement|Sitemap|About US| Contact US: help@patsnap.com