Battery cell winding method and winding equipment
A battery cell and equipment technology, which is applied in the field of battery core winding method and winding equipment, can solve the problems of manual handling and winding process consumption, pole piece die-cutting quality problems, and the inability to adjust again, so as to reduce the scrap rate , Improve production efficiency, save labor costs and plant space
- Summary
- Abstract
- Description
- Claims
- Application Information
AI Technical Summary
Problems solved by technology
Method used
Image
Examples
Embodiment Construction
[0057] Hereinafter, embodiments of the present invention will be described in detail with reference to the drawings.
[0058] Coordinates are used in the following descriptions: Figure 6 Middle, left, and right are left and right, up and down are up and down, the direction vertical to the inside of the paper is back, and vice versa is front. In the present invention, the upstream is the pole piece incoming material direction, and the downstream is the pole piece unloading direction, and the pole piece moves from upstream to downstream.
[0059] Such as figure 2 As shown, a battery winding method includes the following steps: unwinding process, unwinding the coiled pole piece; die-cutting process, die-cutting the unrolled pole piece; winding process, die-cutting The last pole piece is wound into an electric core; wherein, the die-cutting process and the winding process are carried out synchronously.
[0060]It should be noted that the prior art also has an unwinding proces...
PUM
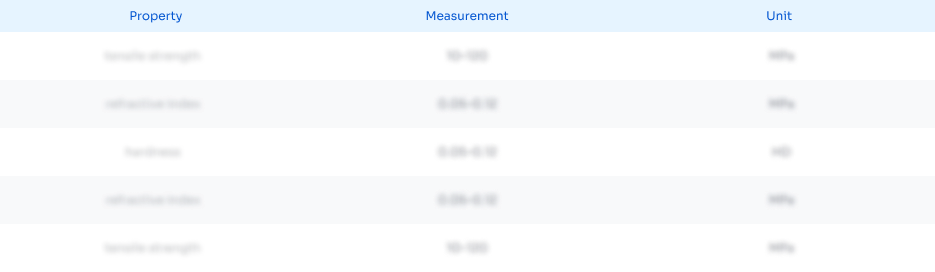
Abstract
Description
Claims
Application Information

- Generate Ideas
- Intellectual Property
- Life Sciences
- Materials
- Tech Scout
- Unparalleled Data Quality
- Higher Quality Content
- 60% Fewer Hallucinations
Browse by: Latest US Patents, China's latest patents, Technical Efficacy Thesaurus, Application Domain, Technology Topic, Popular Technical Reports.
© 2025 PatSnap. All rights reserved.Legal|Privacy policy|Modern Slavery Act Transparency Statement|Sitemap|About US| Contact US: help@patsnap.com