Trimethyl phosphite continuous reduced-pressure rectifying technology
A technology of trimethyl phosphite and vacuum distillation, which is applied in chemical instruments and methods, organic chemistry, compounds of Group 5/15 elements of the periodic table, etc., can solve the problem of insufficient yield and high purity, and reduce tail gas Emissions, improved stability, high exhaust gas recovery effects
- Summary
- Abstract
- Description
- Claims
- Application Information
AI Technical Summary
Problems solved by technology
Method used
Image
Examples
Embodiment Construction
[0026] Such as figure 1 In the continuous vacuum distillation process of trimethyl phosphite shown, the top of the distillation tower is equipped with a first-stage water-cooled condenser and a second-stage brine condenser at about -8°C, and the temperature of the gas phase at the top of the tower is controlled < 0 ℃;
[0027] The gas phase after the two-stage condensation is firstly demistered by the demister, and finally enters the dry screw vacuum pump. The interior of the rectification tower of the control tower is under negative pressure, and its vacuum degree is -88~-90 kPa;
[0028] The condensate pumped by the demister and the vacuum pump flows into the washing tank through the pipeline;
[0029] The liquid condensed by the primary condenser and the secondary condenser enters the rectification reflux tank;
[0030] The condensate flowing into the water washing tank is returned to the rectification tower, and then participates in the distillation process, and so on. ...
PUM
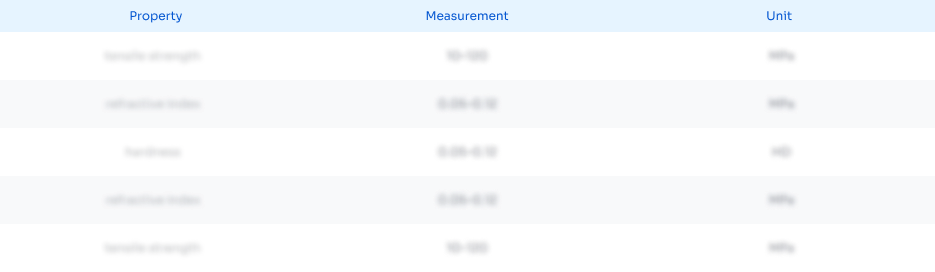
Abstract
Description
Claims
Application Information

- R&D Engineer
- R&D Manager
- IP Professional
- Industry Leading Data Capabilities
- Powerful AI technology
- Patent DNA Extraction
Browse by: Latest US Patents, China's latest patents, Technical Efficacy Thesaurus, Application Domain, Technology Topic, Popular Technical Reports.
© 2024 PatSnap. All rights reserved.Legal|Privacy policy|Modern Slavery Act Transparency Statement|Sitemap|About US| Contact US: help@patsnap.com