Screw-type injection molding machine discharging device structure
A device structure and injection molding machine technology, applied in the field of screw-type injection molding machine blanking device structure, can solve the problems of inability to clean materials, inability to adjust the position of the screw, and affecting operation and use.
- Summary
- Abstract
- Description
- Claims
- Application Information
AI Technical Summary
Problems solved by technology
Method used
Image
Examples
Embodiment Construction
[0022] The following will clearly and completely describe the technical solutions in the embodiments of the present invention with reference to the accompanying drawings in the embodiments of the present invention. Obviously, the described embodiments are only some, not all, embodiments of the present invention.
[0023] Example.
[0024] refer to Figure 1-5, a screw-type injection molding machine blanking device structure, including a blanking funnel 1, the inside of the blanking funnel 1 is movable installed with a rotating motor 2, the output shaft of the rotating motor 2 is fixedly installed with a rotating shaft 5, and both sides of the rotating shaft 5 are A plurality of stirring blades 6 are fixedly installed, and two connecting rods 3 are fixedly installed on the top side of the rotating motor 2, and the tops of the two connecting rods 3 both extend to the top of the feeding funnel 1, and both of them are fixedly installed with a limit block 4 There is a first fixed ...
PUM
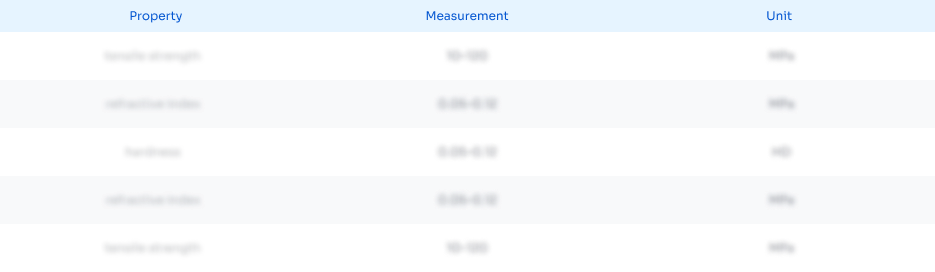
Abstract
Description
Claims
Application Information

- R&D
- Intellectual Property
- Life Sciences
- Materials
- Tech Scout
- Unparalleled Data Quality
- Higher Quality Content
- 60% Fewer Hallucinations
Browse by: Latest US Patents, China's latest patents, Technical Efficacy Thesaurus, Application Domain, Technology Topic, Popular Technical Reports.
© 2025 PatSnap. All rights reserved.Legal|Privacy policy|Modern Slavery Act Transparency Statement|Sitemap|About US| Contact US: help@patsnap.com