Linear stepping motor used for dot matrix image forming and tactile feedback
A linear stepping motor, tactile feedback technology, applied in electrical components, electromechanical devices, propulsion systems, etc., can solve the problems of motor power factor and efficiency limitations, unilateral magnetic pull, complex processing technology, etc., to improve space utilization efficiency, reduced processing difficulty, and simple processing technology
- Summary
- Abstract
- Description
- Claims
- Application Information
AI Technical Summary
Problems solved by technology
Method used
Image
Examples
Embodiment Construction
[0032] The present invention will be further described below in conjunction with drawings and embodiments.
[0033] see figure 1 , the specific implementation of the present invention includes a mover 1, a stator part 2 and a housing 4; the mover 1 and the stator part 2 are respectively installed in the housing 4, the mover 1 is installed in the housing 4 through a guide, and the stator part 2 is set Outside the mover 1 and installed in the housing 4.
[0034] see figure 1 , figure 2 , the housing 4 includes a sleeve-shaped housing 8 and a pin seat 6, a shell through hole 5 is opened in the center of one end face of the shell 8, a needle seat hole 7 is provided beside the shell through hole 5, and a shell is opened in the center of the other end face The threaded hole 9 and the needle seat 6 are installed in the needle seat hole 7 .
[0035] see image 3 , the mover 1 is a stepped shaft structure with several annular grooves uniformly distributed along the axial directio...
PUM
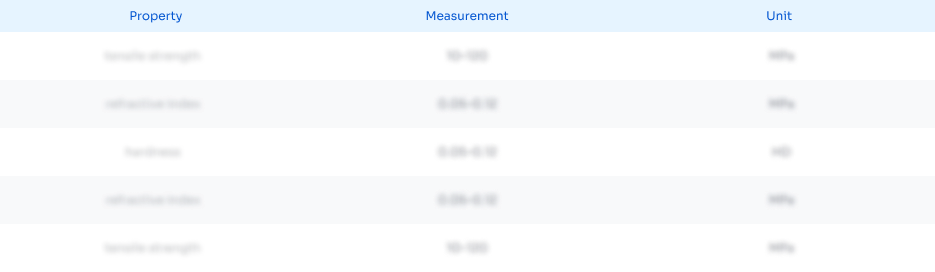
Abstract
Description
Claims
Application Information

- R&D
- Intellectual Property
- Life Sciences
- Materials
- Tech Scout
- Unparalleled Data Quality
- Higher Quality Content
- 60% Fewer Hallucinations
Browse by: Latest US Patents, China's latest patents, Technical Efficacy Thesaurus, Application Domain, Technology Topic, Popular Technical Reports.
© 2025 PatSnap. All rights reserved.Legal|Privacy policy|Modern Slavery Act Transparency Statement|Sitemap|About US| Contact US: help@patsnap.com