A kind of fiber-reinforced cement-based foam insulation board manufacturing process
A fiber-reinforced cement and manufacturing process technology, applied in the direction of manufacturing tools, ceramic molding machines, ceramic molding workshops, etc., can solve the problems of reduced efficiency, easy drop of slurry, complicated process, etc.
- Summary
- Abstract
- Description
- Claims
- Application Information
AI Technical Summary
Problems solved by technology
Method used
Image
Examples
Embodiment Construction
[0058] Best practice:
[0059] A method for manufacturing fiber-reinforced cement-based foam insulation boards, comprising the following steps: first loading materials and putting the prefabricated substrate on the conveying platform of the assembly line, so that the surface of the substrate to be provided with a reinforcement layer faces upward and moves forward with the conveying platform Conveying, during the forward conveying process of the substrate on the conveying platform, the surface of the substrate is subjected to dust removal treatment, slurry laying, mesh cloth laying and synchronous cutting treatment in sequence. The slurry is input to the surface of the substrate, and then the scraper arranged along the transverse direction of the conveying platform is used, so that the slurry is automatically scraped by the scraper when it passes by.
[0060] In this way, the method adopts the flow production line to realize the automatic production and manufacture of the compo...
PUM
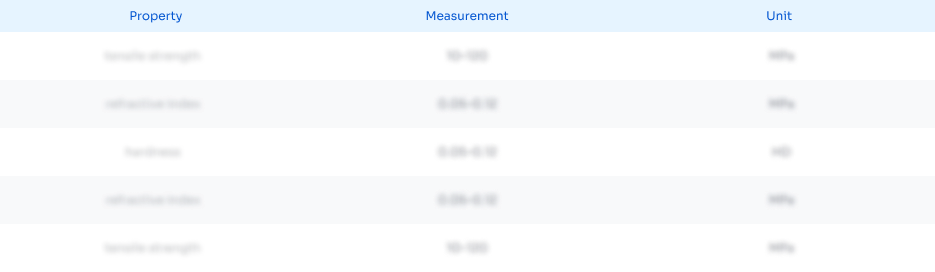
Abstract
Description
Claims
Application Information

- R&D Engineer
- R&D Manager
- IP Professional
- Industry Leading Data Capabilities
- Powerful AI technology
- Patent DNA Extraction
Browse by: Latest US Patents, China's latest patents, Technical Efficacy Thesaurus, Application Domain, Technology Topic, Popular Technical Reports.
© 2024 PatSnap. All rights reserved.Legal|Privacy policy|Modern Slavery Act Transparency Statement|Sitemap|About US| Contact US: help@patsnap.com