A crushing, screening and mixing machine
An all-in-one machine and screening layer technology, which is applied in the fields of filtration, solid separation, agricultural machinery and tools, etc., can solve problems such as unexisted
- Summary
- Abstract
- Description
- Claims
- Application Information
AI Technical Summary
Problems solved by technology
Method used
Image
Examples
Embodiment approach 1
[0029] combine figure 1 -Description of this embodiment, a crushing, screening and stirring integrated machine of this embodiment, the integrated machine includes a body shell 1, and a transmission shaft 2 located inside the body shell 1, a crushing blade 3, a crushing layer bottom plate 4, a stirring paddle 15, Screening layer bottom plate 6, stirring paddle II7, stirring layer bottom plate 8 and filter screen 9; wherein: the top of the body shell 1 is provided with feeding port a; the crushing layer bottom plate 4, screening layer bottom plate 6 and stirring layer bottom plate 8 are It is fixedly connected to the inner wall of the body shell 1 from top to bottom; one end of the transmission shaft 2 is vertically fixed on the center of the bottom wall inside the body shell 1 through a bearing seat, and the end of the other end is fixedly connected to the crushing blade 3; The transmission shaft 2 passes through the stirring layer bottom plate 8, the screening layer bottom pla...
Embodiment approach 2
[0035] This embodiment adds a technical feature controllable passage 11 on the basis of Embodiment 1; the increased controllable passage 11 in this embodiment is located outside the body shell 1, and the entrance of the controllable passage is arranged on the crushing floor bottom plate 4 and the screening Between the bottom plates 6 of the layers, the outlet is arranged between the bottom plates of the screening layer 6 and the bottom plate of the stirring layer 8 .
[0036] The controllable channel 11 of this embodiment connects the screening layer with the stirring layer, and is used to transport the large straw fragments left in the screening layer to the stirring layer through the controllable channel 11, where they are processed by stirring and mixed with other raw materials. (such as glue and / or water), prepared as an intermediate material that requires large-grain straw raw material products.
Embodiment approach 3
[0038] In this embodiment, the technical feature conveyor belt 14 is added on the basis of the first or second embodiment; Inside out.
[0039] The conveyor belt 14 in this embodiment corresponds to the exit position of the material channel IIId, so that the falling materials fall onto the conveyor belt under the action of gravity.
[0040] The conveyor belt 14 added in this embodiment can realize the conveyance of materials, and convey the materials to the next process device.
[0041] The conveyor belt in this embodiment is used to transport materials, and the conveyor belt 14 is an existing product, mainly composed of crawler belts, pulleys and other parts.
PUM
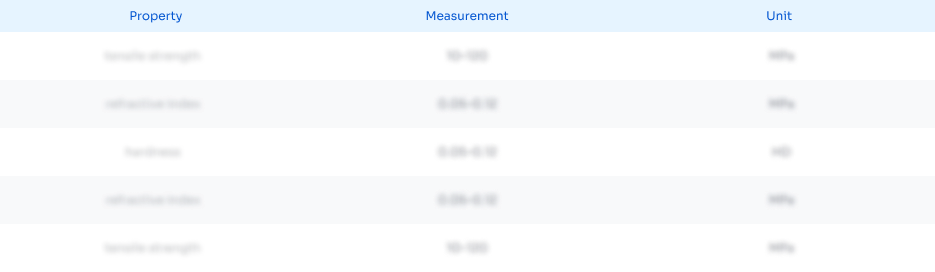
Abstract
Description
Claims
Application Information

- Generate Ideas
- Intellectual Property
- Life Sciences
- Materials
- Tech Scout
- Unparalleled Data Quality
- Higher Quality Content
- 60% Fewer Hallucinations
Browse by: Latest US Patents, China's latest patents, Technical Efficacy Thesaurus, Application Domain, Technology Topic, Popular Technical Reports.
© 2025 PatSnap. All rights reserved.Legal|Privacy policy|Modern Slavery Act Transparency Statement|Sitemap|About US| Contact US: help@patsnap.com