Preparation method of lithium-nickel-cobalt-aluminum composite oxide cathode material for lithium ion battery
A composite oxide and lithium-ion battery technology, applied in battery electrodes, secondary batteries, electrochemical generators, etc., can solve the problems of resource scarcity, low energy density, and low capacity, and achieve simple process routes and excellent cycle performance , The effect of simple process method
- Summary
- Abstract
- Description
- Claims
- Application Information
AI Technical Summary
Benefits of technology
Problems solved by technology
Method used
Image
Examples
Embodiment 1
[0016] Weigh Li 2 CO 3 、Ni 0.815 co 0.15 Al 0.035 (OH) 2 and MnO 2 , Li, Ni 0.815 co 0.15 Al 0.035 , Mn molar ratio is 1.05: 0.95: 0.05, put into the roller ball mill with agate ball medium and fully mix and grind for 5 hours. Heat up at a heating rate of 300°C per hour, roast at a constant temperature for 5 hours after the temperature reaches 400°C, then heat up again, and roast at a constant temperature for 10 hours after the temperature reaches 850°C, then cool naturally to room temperature, and finally mix in a mixing mill and crushing to obtain the lithium-nickel-cobalt-aluminum composite oxide cathode material.
Embodiment 2
[0018] Weigh LiOH, Ni 0.815 co 0.15 Al 0.035 (OH) 2 and MnO 2 , Li, Ni 0.815 co 0.15 Al 0.035 , Mn molar ratio is 1.05: 0.95: 0.05, put into the roller ball mill with agate ball medium and fully mix and grind for 5 hours. Heat up at a heating rate of 300°C per hour, roast at a constant temperature for 4.5 hours after the temperature reaches 500°C, then heat up again, and roast at a constant temperature for 15 hours after the temperature reaches 700°C, then cool naturally to room temperature, and finally in the mixing and grinding equipment Mixed and crushed to obtain lithium-nickel-cobalt-aluminum composite oxide cathode material.
Embodiment 3
[0020] Weigh LiOH, Ni 0.815 co 0.15 Al 0.035 (OH) 2 and MoO 3 , Li, Ni 0.815 co 0.15 Al 0.035 , Mo molar ratio is 1.05:0.98:0.02, put into the roller ball mill that has agate ball medium together and fully mix and grind for 5 hours, after the raw material is mixed evenly, put into sintering sagger, after introducing protective gas in the atmosphere furnace, with Heat up at a heating rate of 300°C per hour, roast at a constant temperature for 4 hours after the temperature reaches 450°C, then heat up again, and roast at a constant temperature for 20 hours after the temperature reaches 780°C, then cool naturally to room temperature, and finally mix in a mixing mill and crushing to obtain the lithium-nickel-cobalt-aluminum composite oxide cathode material.
PUM
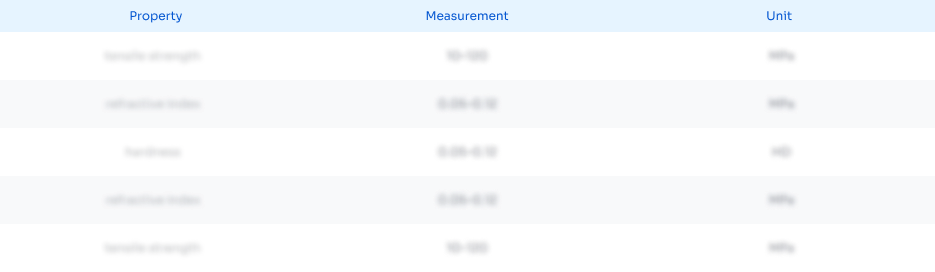
Abstract
Description
Claims
Application Information

- Generate Ideas
- Intellectual Property
- Life Sciences
- Materials
- Tech Scout
- Unparalleled Data Quality
- Higher Quality Content
- 60% Fewer Hallucinations
Browse by: Latest US Patents, China's latest patents, Technical Efficacy Thesaurus, Application Domain, Technology Topic, Popular Technical Reports.
© 2025 PatSnap. All rights reserved.Legal|Privacy policy|Modern Slavery Act Transparency Statement|Sitemap|About US| Contact US: help@patsnap.com