Cement foaming heat-insulating decorative integrated board and production method thereof
A cement foaming and production method technology, which is applied in the field of building exterior wall decoration, can solve the problems of not being able to simultaneously satisfy heat preservation, sound insulation, fire prevention, high construction difficulty, and single function, achieve good fire protection function, convenient construction, and improve work efficiency Effect
- Summary
- Abstract
- Description
- Claims
- Application Information
AI Technical Summary
Problems solved by technology
Method used
Examples
Embodiment 1
[0029] In this embodiment, the thickness ratio of the base layer, the inorganic finish layer and the finish layer is 1:1.5:0.3.
[0030]Take 75% of slaked lime, 10% of deionized water, 10% of water-based silica sol, 2% of organosiloxane, and 3% of polyacrylate in a mixer and mix them for more than 30 minutes until they are completely mixed to obtain the raw material of the base layer; SiO 2 46%, nano-Al 2 o 3 4%, Nano TiO 2 6%, water-based acrylic emulsion 14%, water-based silica sol 10%, polyacrylate 3%, organosiloxane 2%, deionized water 15%, mixed in a stirrer and stirred at 600 rpm for more than 60 minutes to Completely mix evenly to obtain the raw material of the inorganic finish layer; take 70% of deionized water, 12% of acrylic resin, 1.5% of general industrial antifungal agent, 1.5% of general industrial preservative, 2% of organosiloxane, 10% of wax liquid, Mix 3% polyacrylate in a mixer and stir for more than 30 minutes until completely mixed to obtain the raw ma...
Embodiment 2
[0033] In this embodiment, the thickness ratio of the base layer, the inorganic finish layer and the finish layer is 1:2.2:0.4.
[0034] Take 68% of slaked lime, 13% of deionized water, 12% of water-based silica sol, 3% of organosiloxane, and 4% of polyacrylate in a blender and mix them for more than 30 minutes until they are completely mixed to obtain the raw material of the base layer; SiO 2 50%, nano-Al 2 o 3 5%, Nano TiO 2 7%, water-based acrylic emulsion 11%, water-based silica sol 12%, polyacrylate 4%, organosiloxane 2%, deionized water 9%, mixed in a stirrer and stirred at 800 rpm for more than 60 minutes to Completely mix evenly to obtain the raw material of the inorganic finish layer; take 65% of deionized water, 10% of acrylic resin, 3% of general industrial antifungal agent, 3% of general industrial antiseptic, 3% of organosiloxane, 14% of wax liquid, Mix 2% polyacrylate in a mixer and stir for more than 30 minutes until completely mixed to obtain the raw materi...
Embodiment 3
[0037] In this embodiment, the thickness ratio of the base layer, the inorganic finish layer and the finish layer is 1:3:0.5.
[0038] Take 60% of slaked lime, 17% of deionized water, 14% of water-based silica sol, 4% of organosiloxane, and 5% of polyacrylate in a blender and mix them for more than 30 minutes until they are completely mixed to obtain the raw material of the base layer; SiO 2 53%, nano-Al 2 o 3 5.5%, Nano TiO 2 7.5%, water-based acrylic emulsion 12%, water-based silica sol 11%, polyacrylate 3.5%, organosiloxane 2.5%, deionized water 5%, mixed in a stirrer and stirred at 1000 rpm for more than 60 minutes to Completely mix evenly to obtain the raw material of the inorganic finish layer; take 60% of deionized water, 15% of acrylic resin, 2% of general industrial antifungal agent, 2% of general industrial preservative, 4% of organosiloxane, 15% of wax liquid, Mix 2% polyacrylate in a mixer and stir for more than 30 minutes until completely mixed to obtain the r...
PUM
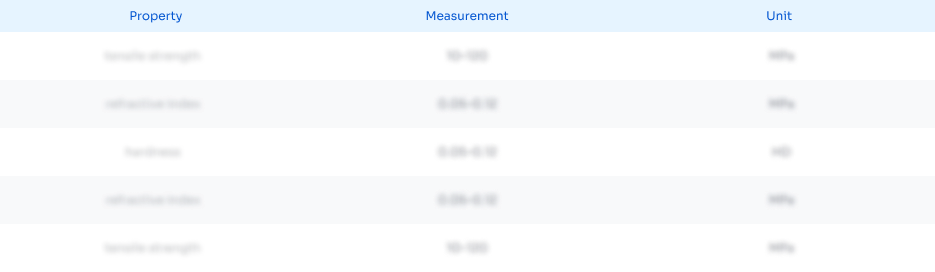
Abstract
Description
Claims
Application Information

- R&D Engineer
- R&D Manager
- IP Professional
- Industry Leading Data Capabilities
- Powerful AI technology
- Patent DNA Extraction
Browse by: Latest US Patents, China's latest patents, Technical Efficacy Thesaurus, Application Domain, Technology Topic, Popular Technical Reports.
© 2024 PatSnap. All rights reserved.Legal|Privacy policy|Modern Slavery Act Transparency Statement|Sitemap|About US| Contact US: help@patsnap.com