Single piezoelectric stack-based inertial nanometer stepping motor
A piezoelectric stack, stepper motor technology, applied in piezoelectric effect/electrostrictive or magnetostrictive motors, electrical components, generators/motors, etc., can solve the problem of increasing control difficulty, weak overall rigidity, etc. problems, to achieve the effect of improving rigidity and stepping accuracy, strong structural rigidity, and easy realization of the structure
- Summary
- Abstract
- Description
- Claims
- Application Information
AI Technical Summary
Problems solved by technology
Method used
Image
Examples
Embodiment Construction
[0025] The present invention is described in further detail now in conjunction with accompanying drawing.
[0026] Combined with the micro-nano motor based on the shear piezoelectric stack disclosed in the invention with the publication number CN107086812ACN and the name "a micro-nano motor based on the shear piezoelectric stack", the present invention sticks the inner wall of the original guide groove Four silicon nitride balls are connected to reduce the friction between them and the sliding rod. At the same time, the present invention only uses one piezoelectric stack for inertial drive. By adjusting the pressing force of the beryllium copper spring on the sliding rod, The maximum static friction force between the force transmission block and the sliding rod is adjusted, the friction force is adjustable, and the overall structure is simple and easy to realize.
[0027] Such as figure 1 As shown, an inertial nanometer stepper motor based on a single piezoelectric stack in t...
PUM
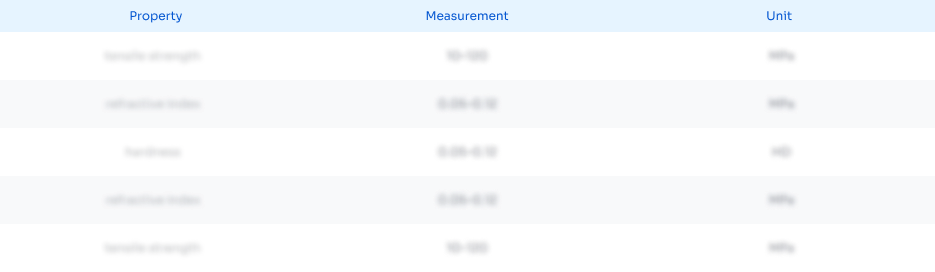
Abstract
Description
Claims
Application Information

- R&D
- Intellectual Property
- Life Sciences
- Materials
- Tech Scout
- Unparalleled Data Quality
- Higher Quality Content
- 60% Fewer Hallucinations
Browse by: Latest US Patents, China's latest patents, Technical Efficacy Thesaurus, Application Domain, Technology Topic, Popular Technical Reports.
© 2025 PatSnap. All rights reserved.Legal|Privacy policy|Modern Slavery Act Transparency Statement|Sitemap|About US| Contact US: help@patsnap.com