Multi-support piezoelectric dynamometer calibration method
A calibration method and technology of a dynamometer, applied in the direction of force/torque/power measuring instrument calibration/testing, instruments, measuring devices, etc., can solve the problems that the test accuracy does not meet the test requirements, etc., and achieve the improvement of calibration accuracy and reliability sex, the effect of increasing the absolute value
- Summary
- Abstract
- Description
- Claims
- Application Information
AI Technical Summary
Problems solved by technology
Method used
Image
Examples
Embodiment 1
[0035] Embodiment 1, the object 6 to be calibrated in the present invention is a four-point piezoelectric force measuring instrument, the size of the upper plate is 186×186×35mm, the size of the lower plate is 186×186×20mm, and the size of the four piezoelectric force sensors is 40× 40×14mm, the layout spacing is 140mm; the calibration system includes a standard force measuring ring 93618 with a range of 6000N, 4 Kistler charge amplifiers 5018, a data acquisition card DT9804, and a computer with Dewesoft 6 installed.
[0036] The first step is to calibrate the force gauge
[0037]Fix the four-point piezoelectric dynamometer (6) on the base (5) of the loading platform by bolts, so that the diagonal line of the upper plate of the dynamometer is located on the main force moving surface (7), and the liquid level (14) Place it on the guide rail (10), adjust the lock nut (11) to make the guide rail (10) in the horizontal direction, turn the hand wheel (15), and move the main directi...
PUM
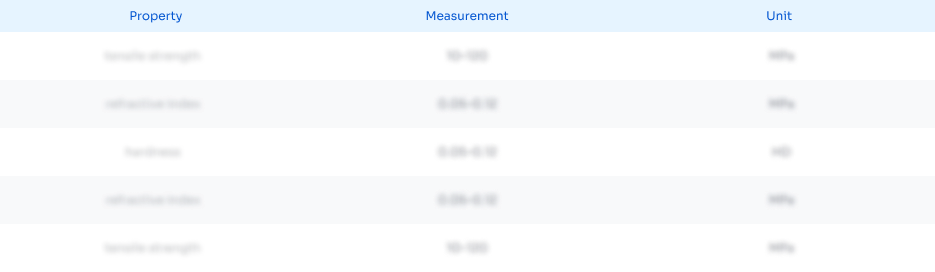
Abstract
Description
Claims
Application Information

- Generate Ideas
- Intellectual Property
- Life Sciences
- Materials
- Tech Scout
- Unparalleled Data Quality
- Higher Quality Content
- 60% Fewer Hallucinations
Browse by: Latest US Patents, China's latest patents, Technical Efficacy Thesaurus, Application Domain, Technology Topic, Popular Technical Reports.
© 2025 PatSnap. All rights reserved.Legal|Privacy policy|Modern Slavery Act Transparency Statement|Sitemap|About US| Contact US: help@patsnap.com