Winding drum welding method and winding drum
A welding method and reel technology, which are applied in the field of reel manufacturing, can solve the problem of easy deformation of reels, and achieve the effects of reducing welding stress, ensuring the quality of welding seams, and reducing welding deformation.
- Summary
- Abstract
- Description
- Claims
- Application Information
AI Technical Summary
Problems solved by technology
Method used
Image
Examples
Embodiment Construction
[0031] In order to make the object, technical solution and advantages of the present invention clearer, the implementation manner of the present invention will be further described in detail below in conjunction with the accompanying drawings.
[0032] An embodiment of the present invention provides a drum welding method, which is especially suitable for welding super-large drums with a diameter of more than 3000 mm. figure 1 It is a flow chart of the drum welding method provided by the embodiment of the present invention, such as figure 1 As shown, the drum welding method includes:
[0033] Step 101: Provide a shell and two spoke assemblies.
[0034] figure 2 It is a front sectional view of the cylinder shell provided by the embodiment of the present invention. Such as figure 2 As shown, the shell 1 is a cylindrical structure, and the thickness of the shell is greater than 80 mm. In this embodiment, the material of the shell may be steel, such as Q345.
[0035] In thi...
PUM
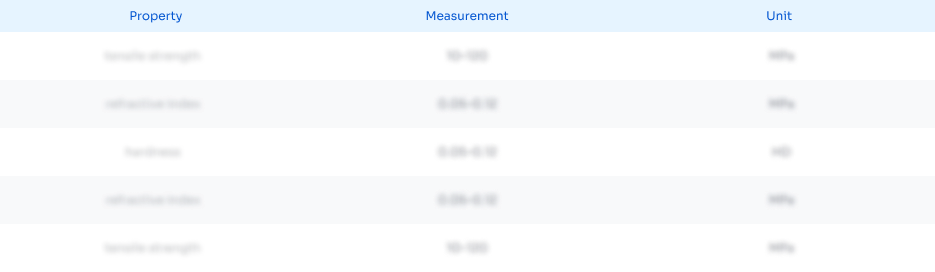
Abstract
Description
Claims
Application Information

- R&D
- Intellectual Property
- Life Sciences
- Materials
- Tech Scout
- Unparalleled Data Quality
- Higher Quality Content
- 60% Fewer Hallucinations
Browse by: Latest US Patents, China's latest patents, Technical Efficacy Thesaurus, Application Domain, Technology Topic, Popular Technical Reports.
© 2025 PatSnap. All rights reserved.Legal|Privacy policy|Modern Slavery Act Transparency Statement|Sitemap|About US| Contact US: help@patsnap.com