Model test piece design method of metal-wing main box section bending rigidity test
A technology of model test and design method, applied in the field of aircraft structure rigidity test, can solve the problems of long production and test cycle, large test piece size and high test conditions, and achieve the effect of shortening design cycle, saving design cost and low production cost
- Summary
- Abstract
- Description
- Claims
- Application Information
AI Technical Summary
Problems solved by technology
Method used
Image
Examples
Embodiment Construction
[0039] In order to make the objectives, technical solutions and advantages of the present invention clearer, the technical solutions in the embodiments of the present invention will be described in more detail below in conjunction with the drawings in the embodiments of the present invention.
[0040] The model test piece design method for the rigidity test of the aircraft metal wing main box section of the present invention is suitable for the design of the large aircraft metal wing main box section, and it is the first time that a model test piece using an equivalent wing wall plate is used to reversely obtain an actual large aircraft The method of bending stiffness of the main box section of the metal wing realizes the test of the bending stiffness of the main box section of the metal wing of a large aircraft through the model test piece, and solves the problem of large size of the stiffness test piece of the main box section of the metal wing of a large aircraft, a long prod...
PUM
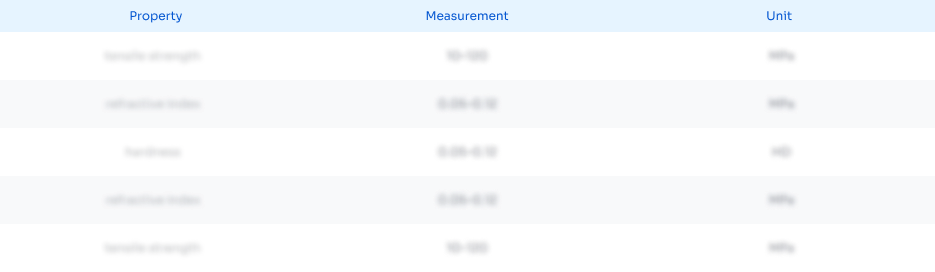
Abstract
Description
Claims
Application Information

- R&D
- Intellectual Property
- Life Sciences
- Materials
- Tech Scout
- Unparalleled Data Quality
- Higher Quality Content
- 60% Fewer Hallucinations
Browse by: Latest US Patents, China's latest patents, Technical Efficacy Thesaurus, Application Domain, Technology Topic, Popular Technical Reports.
© 2025 PatSnap. All rights reserved.Legal|Privacy policy|Modern Slavery Act Transparency Statement|Sitemap|About US| Contact US: help@patsnap.com